Exploring Key Factors for Selecting H13 Steel for Die Applications!
Selecting the right H13 hot work tool steel for die applications involves understanding its properties, assessing your operational requirements, and choosing a reliable supplier. Its unmatched combination of toughness, thermal resistance, and durability makes it an indispensable material for demanding applications. By following the guidelines outlined in this article, you can make an informed decision that ensures optimal die performance and cost-effectiveness.
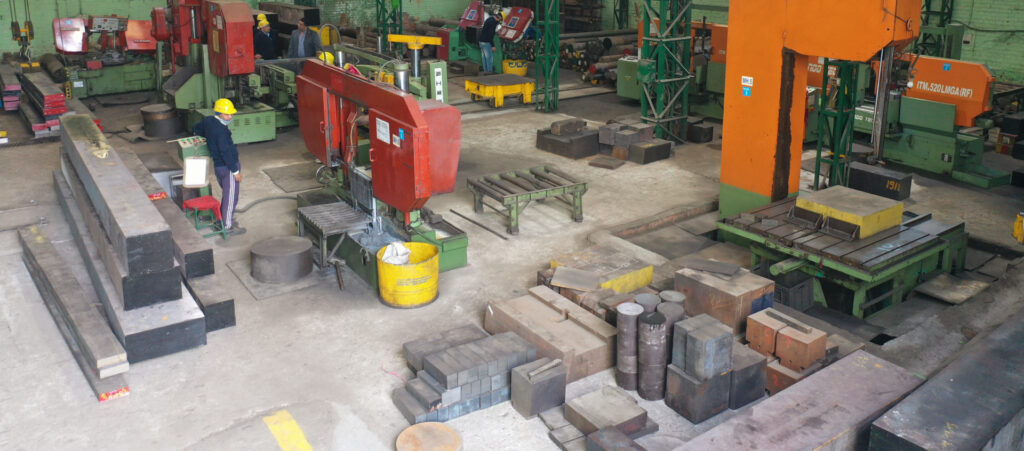
Choosing the right steel for die-making is like laying a solid foundation for a building. It’s the cornerstone that ensures durability, efficiency, and precision in manufacturing processes. Among the wide range of tool steels, H13 hot work tool steel stands out as a preferred choice for die applications. Why? Its excellent combination of toughness, temperature resistance, and durability makes it a favorite across various industries, from automotive to aerospace.
In this guide, we’ll explore everything you need to know about selecting H13 hot work tool steel for your die applications, including what makes it unique and the key factors to consider.
Understanding H13 Hot Work Tool Steel
What is H13 Steel?
H13 is a chromium-molybdenum-vanadium alloy steel, classified as a hot work tool steel. It is specially designed to endure high temperatures, resist thermal fatigue, and maintain structural integrity even under demanding conditions.
Key Properties of H13 Steel
- High Thermal Resistance: Withstands extreme heat without losing strength.
- Toughness and Durability: Handles impact and wear during heavy-duty operations.
- Thermal Conductivity: Promotes effective heat dissipation, preventing die failure.
- Wear Resistance: Resists abrasion and erosion, extending die life.
Advantages of H13 for Die Applications
H13’s balance of strength, hardness, and temperature resistance makes it ideal for hot-working operations such as forging, extrusion, and die-casting. It ensures fewer downtimes, consistent production quality, and reduced replacement costs.
Key Factors to Consider When Selecting H13 Steel for Die Applications
Temperature Resistance
The performance of dies often depends on their ability to handle extreme operating temperatures. H13 steel excels in environments where tools are exposed to temperatures up to 600°C (1112°F) or higher. Industries such as die-casting and forging heavily rely on H13 for its capacity to endure thermal cycling without cracking or deforming.
Hardness and Strength
Hardness directly influences a die’s wear resistance and operational life. H13 steel offers a Rockwell hardness range of 48-54 HRC, making it suitable for heavy-load applications. A well-balanced hardness ensures that the die can withstand repeated impacts and prolonged usage without succumbing to premature wear.
Thermal Conductivity
Heat buildup in dies can lead to dimensional changes, premature wear, and reduced production efficiency. H13’s excellent thermal conductivity ensures uniform heat distribution, which not only protects the die but also enhances the quality of the output by reducing imperfections in the finished product.
Toughness and Impact Resistance
Dies often face high pressure and sudden impacts during operations. H13 steel’s inherent toughness and impact resistance make it capable of absorbing shocks without cracking. This property is especially critical for industries such as automotive manufacturing, where precision and reliability are paramount.
Pre-Treatment and Heat Treatment of H13 Steel
The performance of H13 steel depends significantly on proper pre-treatment and heat treatment. Pre-treatment involves processes like annealing, which enhances machinability. Heat treatment, on the other hand, optimizes hardness, strength, and thermal resistance. Key heat treatment steps include hardening, tempering, and stress relieving, all tailored to the die’s intended application.
Evaluating Quality Standards for H13 Steel
To ensure you’re investing in high-quality H13 steel, look for certifications like ASTM A681 or DIN 1.2344. Premium-grade H13 steel should exhibit uniform composition, minimal impurities, and consistent mechanical properties. It’s advisable to work with reputable suppliers who provide material test certificates (MTC) to guarantee quality.
Applications of H13 Hot Work Tool Steel in Die-Making
H13 steel is used across a broad range of die-making applications, including:
- Die-Casting Dies: Withstands molten metal temperatures and repetitive cooling cycles.
- Forging Dies: Handles high-impact loads without deforming.
- Extrusion Dies: Provides excellent resistance to thermal wear and pressure.
Tips for Purchasing H13 Steel
When buying H13 steel, consider these tips:
- Source from trusted suppliers like Virat Special Steels for consistent quality.
- Verify certifications and specifications.
- Request samples or small batches for testing before large-scale purchase.
Maintenance of H13 Steel Dies
Regular maintenance can significantly extend the life of H13 steel dies. Periodic inspections help identify early signs of wear, such as cracking or pitting. Implementing proper cooling cycles and using lubricants can further enhance the die’s performance and longevity.
FAQs
- What makes H13 steel unique for die-making?
Its exceptional balance of toughness, thermal resistance, and wear resistance. - How does heat treatment impact H13 steel performance?
Heat treatment optimizes hardness and toughness, enhancing durability. - What industries benefit the most from using H13 steel?
Industries like die-casting, forging, and extrusion heavily rely on H13 steel. - How to identify high-quality H13 steel suppliers?
Look for certifications, test reports, and a proven track record of reliability. - What are the common challenges when using H13 dies?
Issues like thermal fatigue and cracking can arise if not properly maintained.
Mode of Supply:
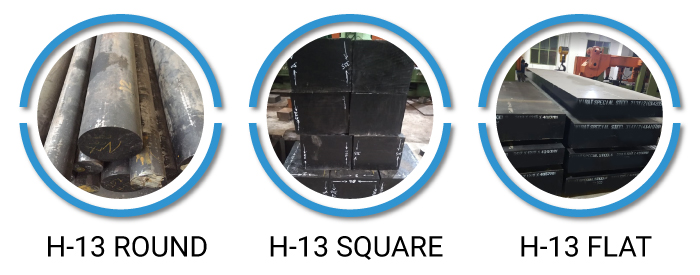
Virat Special Steels is the largest Supplier & Stockiest of H13 Steel in India. Consult our team who will assist you for H-13/ DIN 2344 / AISI H13 steel query. https://www.viratsteels.com/h13.html
Size Range in Forged / Rolled Bars:
Rounds: 13mm Dia to 1500mm Dia
Rectangular: Thickness 13mm – 500mm / Width 13mm to 1500mm
For more information or to discuss your steel needs, Virat Special Steels invites you to reach out through their contact details provided, ensuring a professional and informative experience.
Any further queries feel free to contact us :
🌐https://www.viratsteel.in 📬 info@viratsteels.com ☎+91 98140-21775