Comparing DB6 Steel vs H13 Steel: Key Differences and Uses
In the world of tool steels, DB6 and H13 stand out as two popular choices. Known for their reliability and performance, these steels serve a variety of industries such as automotive, aerospace, and die-making. But how do these two materials compare, and what are their most suitable applications?
Let’s dive deep into their properties, differences, and uses to help you make an informed decision.
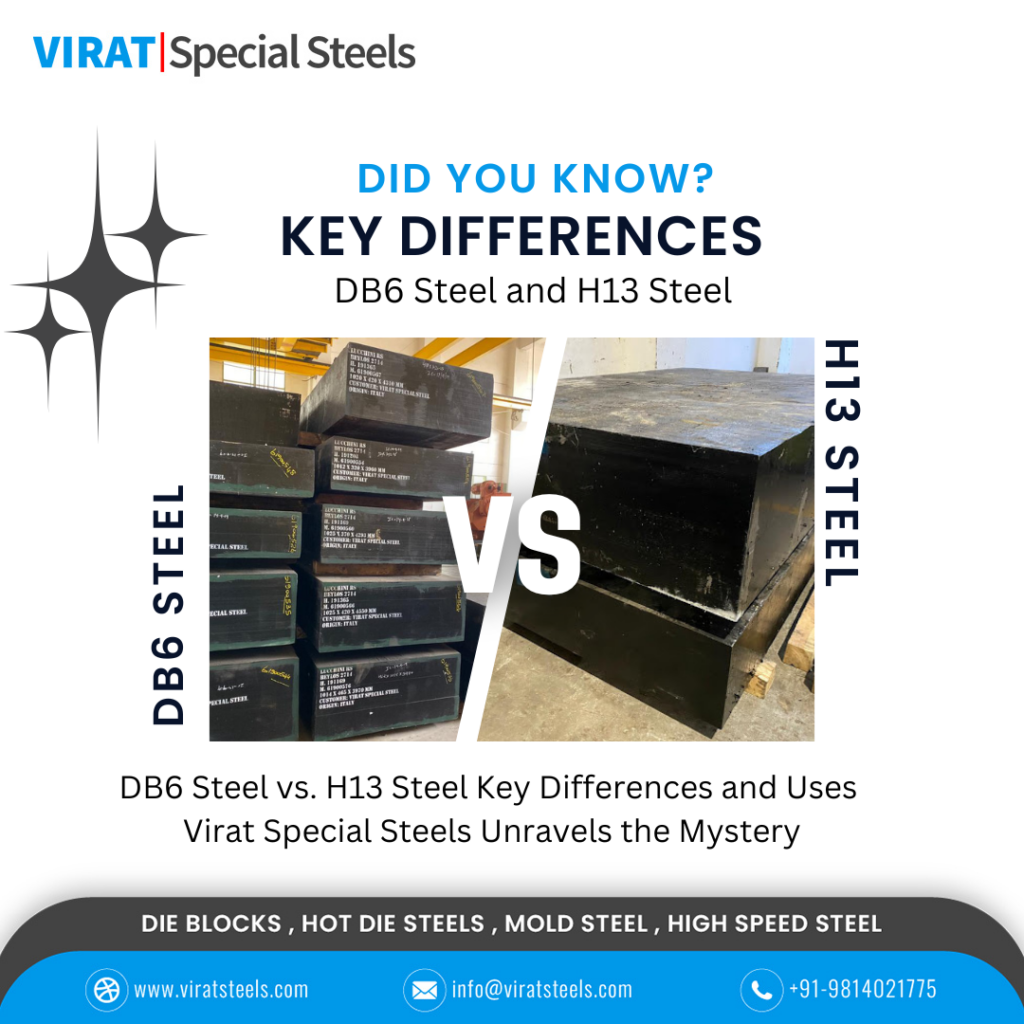
1. Understanding DB6 Steel
DB6 steel, or D6 steel, is a high-carbon, high-chromium tool steel. It boasts impressive wear resistance and is often utilized in applications requiring durability and hardness.
Key Properties of DB6 Steel
- High Hardness: DB6 excels in maintaining high hardness even under stress.
- Abrasion Resistance: Its chromium-rich composition offers superb abrasion resistance, making it ideal for demanding environments.
- Dimensional Stability: It resists deformation under heat and mechanical pressure.
Applications of DB6 Steel
DB6 steel is primarily used in:
- Cold-working applications like die casting molds
- Punches and cutting tools
- Deep-drawing dies
It is a go-to choice for processes requiring precision and wear resistance.
2. Understanding H13 Steel
H13 steel is a chromium-molybdenum alloy with exceptional toughness and versatility. It performs well across a wide temperature range, making it an industry favorite.
Key Properties of H13 Steel
- High Thermal Strength: H13 retains its mechanical strength even at elevated temperatures.
- Shock Resistance: Excellent impact resistance makes it ideal for heavy-duty applications.
- Versatility: Suitable for both hot-working and cold-working processes.
Applications of H13 Steel
Commonly, H13 steel is used in:
- Injection molding dies
- Hot forging dies
- Aerospace and automotive components
Its versatility makes it indispensable for industries where temperature changes are a factor.
3. Composition Comparison: DB6 vs. H13
Understanding the chemical composition of both steels is crucial for identifying their potential use cases.
Element | DB6 Steel | H13 Steel |
Chromium | High (12%–14%) | Moderate (4.75%–5.50%) |
Carbon | High (1.4%–1.6%) | Lower (0.32%–0.45%) |
Molybdenum | Low | High (1.2%–1.5%) |
Vanadium | Trace | Present (0.8%–1.2%) |
Silicon | Moderate (0.4%–0.7%) | Low (0.8%–1.0%) |
The higher chromium content in DB6 gives it better wear resistance, while the molybdenum in H13 offers enhanced thermal stability and toughness.
4. Mechanical Properties Comparison
Property | DB6 Steel | H13 Steel |
Hardness | Extremely high | High |
Thermal Resistance | Moderate | Excellent |
Wear Resistance | Superior | Good |
Toughness | Moderate | Superior |
DB6 excels in situations demanding high wear resistance and hardness, while H13’s toughness makes it better suited for impact-heavy and high-heat applications.
5. Key Differences Between DB6 and H13 Steel
Feature | DB6 Steel | H13 Steel |
Best for | Cold-working applications | Hot-working and high-impact jobs |
Thermal Capability | Limited | Suitable for high temperatures |
Impact Resistance | Lower | Higher |
Corrosion Resistance | High | Moderate |
These differences highlight how each steel caters to specific industrial needs.
6. Choosing the Right Steel: DB6 vs. H13
When deciding between DB6 and H13, consider:
- Work Conditions: Is the application exposed to high temperatures or high wear?
- Desired Properties: Do you need exceptional wear resistance (DB6) or superior toughness (H13)?
- Budget: H13 is generally more cost-effective for its versatility, but DB6 offers long-term durability.
7. Common Industries and Their Preference
Industry | Preferred Steel | Reason |
Tool & Die Making | DB6 Steel | Excellent wear resistance for extended tool life. |
Automotive | H13 Steel | Handles the heat and stress of forging components. |
Aerospace | H13 Steel | Resilient to thermal fatigue in extreme environments. |
8. Cost Implications
- DB6 Steel: Higher cost due to chromium and specialized applications.
- H13 Steel: More affordable, widely available, and multi-functional.
9. Maintenance and Longevity
Proper care ensures both steels perform optimally.
- DB6: Periodic inspection for cracks and maintaining cool temperatures can extend its lifespan.
- H13: Regular thermal treatments enhance its resilience against wear and fatigue.
10. Final Verdict
Both DB6 and H13 steels have their strengths. While DB6’s wear resistance makes it unbeatable for cold applications, H13’s versatility shines in demanding thermal environments. The final choice depends on your project’s specific requirements.
Conclusion
Choosing between DB6 and H13 steel isn’t a one-size-fits-all decision. By understanding their unique properties and applications, you can match the steel to your manufacturing needs effectively. Whether it’s the durability of DB6 or the robustness of H13, both steels promise performance when used in the right setting.
FAQs
- What makes H13 suitable for hot applications?
H13’s composition with molybdenum and vanadium gives it superior thermal stability and resistance to heat deformation. - Is DB6 more expensive than H13?
Yes, DB6 typically costs more due to its specialized high-chromium content and niche applications. - Can H13 steel be used for cold applications?
Yes, but DB6 steel is better for cold applications due to its higher wear resistance. - Which steel offers better impact resistance?
H13 steel is superior in impact resistance, thanks to its toughness and balanced alloy composition. - How can I maintain DB6 steel?
Regular inspections for wear and avoiding prolonged exposure to high temperatures can maximize DB6’s lifespan.