H13 Steel for Die Casting: Key Benefits You Should Know
H13 steel stands as a cornerstone in the die casting industry. Known for its exceptional heat resistance and toughness, this versatile hot-work tool steel is widely used in demanding environments. As die casting often involves high-pressure and extreme thermal conditions, choosing the right material for dies is critical. Enter H13 steel – the ultimate material to enhance durability, improve performance, and maximize efficiency in casting operations.
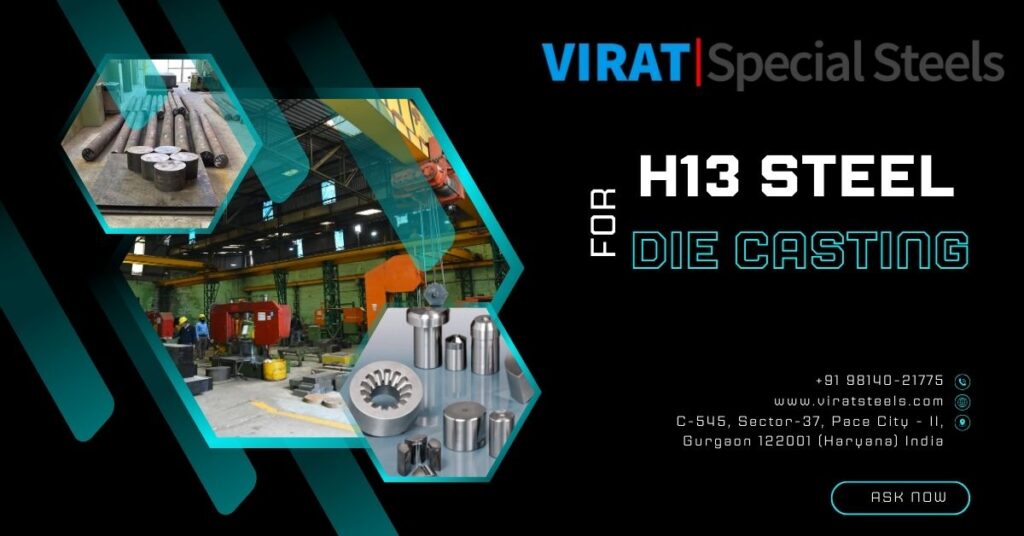
What sets H13 steel apart from the rest? Its outstanding properties make it highly sought after for both small-scale and large-scale die casting applications. But let’s dig deeper into what makes it so special.
Composition and Properties of H13 Steel
Chemical Composition
H13 steel is an alloy comprising a mix of critical elements that optimize its performance. Here’s a breakdown of its main components:
- Chromium (5%): Enhances corrosion resistance.
- Molybdenum (1.4%): Improves hardness and high-temperature strength.
- Vanadium (1%): Increases wear resistance and toughness.
- Carbon (0.4%): Adds strength and hardenability.
- Silicon (1%): Boosts resistance to oxidation.
Mechanical Properties
H13 steel is known for its high tensile strength, ductility, and excellent thermal conductivity. These properties ensure the material remains reliable under rigorous operating conditions. Additionally, H13 steel demonstrates impressive hardenability, making it an ideal choice for precision die applications.
What Makes H13 Steel Ideal for Die Casting?
Thermal Stability
One of the standout features of H13 steel is its remarkable thermal stability. In die casting, molds must endure rapid temperature fluctuations without cracking or deforming. H13’s ability to retain strength at elevated temperatures makes it indispensable.
Resistance to Thermal Fatigue
When dies repeatedly heat and cool during the casting cycle, they are prone to thermal fatigue. H13 steel offers resistance to such stresses, extending the lifespan of the tooling and reducing operational downtime.
Key Benefits of H13 Steel in Die Casting
1. Durability Under High Temperatures
Die casting requires materials that can handle intense heat without losing integrity. H13 steel delivers exceptional performance in such scenarios, maintaining structural stability even under prolonged exposure to molten metals.
2. Excellent Wear Resistance
The abrasive nature of die casting operations can wear down weaker materials quickly. With its robust wear resistance, H13 steel minimizes maintenance needs and offers long-lasting performance.
3. Cost-Effectiveness in Long Production Runs
Although the initial investment in H13 steel may be higher, its durability and resistance to damage translate into significant cost savings over time. Long production cycles benefit greatly from its ability to perform without frequent replacements or repairs.
Longevity and Durability of H13 Steel Dies
Improved Tool Life
When it comes to tooling materials, longevity matters. H13 steel excels in providing longer service life, reducing the need for frequent replacements. Its resilience against wear and deformation significantly adds to the efficiency of the production process.
Resistance to Deformation
Under the extreme pressures of die casting, lesser materials may deform, leading to suboptimal casting results. H13 steel’s resistance to deformation ensures precision and repeatability across countless cycles.
Challenges and Limitations of H13 Steel
Cost Considerations
While H13 steel is cost-effective in the long run, its upfront cost may deter smaller manufacturers. Investing in H13 tooling requires foresight and planning to maximize its return on investment.
Potential Limitations in Specific Environments
H13 steel thrives under high temperatures, but in applications involving extremely corrosive materials or environments, alternative alloys with specific properties might be better suited.
Future Trends in Die Casting Using H13 Steel
Advances in Steel Technologies
Research and innovation are leading to improved formulations of H13 steel with enhanced properties like higher thermal resistance and lower environmental impact. Such developments will further cement H13’s place in the future of die casting.
Emerging Applications and Industries
With rapid advancements in technology, H13 steel’s applications are expanding beyond traditional die casting. Sectors like robotics and renewable energy are beginning to explore its potential, showcasing the steel’s enduring versatility.
Conclusion
H13 steel has revolutionized the die casting industry with its unmatched thermal stability, wear resistance, and adaptability. From improving tool longevity to delivering consistent, high-quality results, it’s clear why this alloy is the material of choice for demanding casting operations. By investing in H13 steel, manufacturers can elevate their production standards, reduce costs over time, and lead the way in sustainable manufacturing.
FAQs
1. Why is H13 steel commonly used in die casting?
H13 steel is ideal for die casting due to its thermal stability, resistance to wear and deformation, and long service life. It is especially effective in high-temperature, high-pressure applications.
2. Can H13 steel be recycled?
Yes, H13 steel is 100% recyclable, making it a sustainable choice for manufacturers committed to reducing waste.
3. How does H13 steel compare to P20 steel?
H13 steel offers superior heat resistance and durability compared to P20, making it more suitable for demanding die casting operations.
4. What industries use H13 steel dies?
H13 steel is widely used in industries such as automotive, aerospace, electronics, and general manufacturing for creating precision die-cast components.
5. What maintenance is required for H13 steel dies?
Regular preventive maintenance, including cleaning, inspections, and refurbishments, is essential to extend the lifespan of H13 steel dies and ensure optimal performance.
Virat Special Steels: A Leader in H13 Steel Supplies
Virat Special Steels is a renowned name in delivering high-quality tool steels, including H13. With decades of industry expertise, Virat has built a reputation for reliability and superior service. Industries across automotive, aerospace, and plastic molding trust Virat for their steel requirements.
Virat Special Steels is the largest Supplier & Stockiest of H13 Steel in India. Consult our team who will assist you for H-13/ DIN 2344 / AISI H13 steel query. https://www.viratsteels.com/h13.html
Size Range in Forged / Rolled Bars:
Rounds: 13mm Dia to 1500mm Dia
Rectangular: Thickness 13mm – 500mm / Width 13mm to 1500mm
For more information or to discuss your steel needs, Virat Special Steels invites you to reach out through their contact details provided, ensuring a professional and informative experience.
Any further queries feel free to contact us :
🌐https://www.viratsteel.in 📬 info@viratsteels.com ☎+91 98140-21775
The Role of DIN 2714 Steel in Forging Industries
The forging industry plays a pivotal role in manufacturing, producing components that form the backbone of various sectors such as automotive, aerospace, construction, and heavy machinery. One material that has emerged as a cornerstone of the forging process is DIN 2714 steel. Renowned for its exceptional properties, DIN 2714 is a hot work tool steel that meets the rigorous demands of forging operations. This blog delves into the characteristics, applications, and benefits of DIN 2714 steel, highlighting its indispensability in the forging industry.
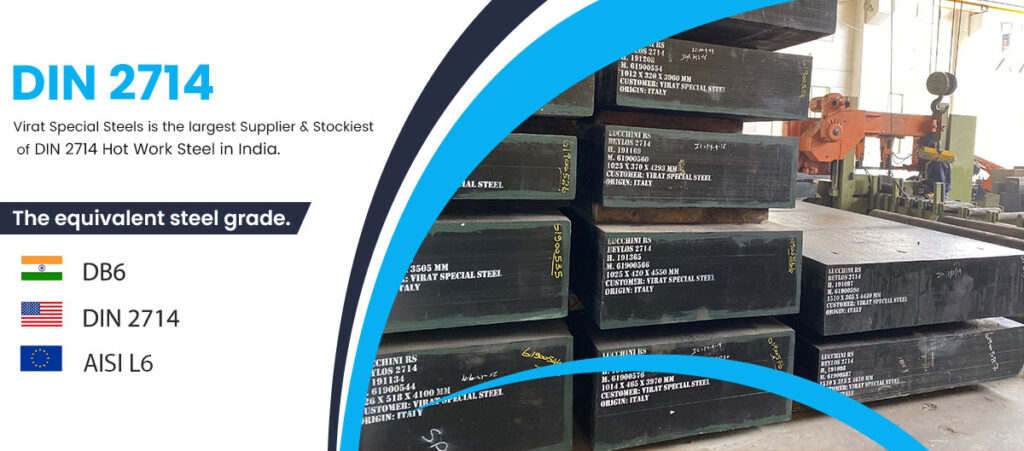
Understanding DIN 2714 Steel
DIN 2714 is a German-standard steel, widely recognized for its high wear resistance, toughness, and thermal stability. It belongs to the family of alloyed steels that exhibit excellent mechanical properties, making it ideal for use in hot forging tools. The composition of DIN 2714 typically includes:
Carbon (C): Contributing to hardness and strength.
Silicon (Si): Enhancing heat resistance.
Manganese (Mn): Improving toughness and hardenability.
Chromium (Cr): Providing corrosion resistance and strength.
Molybdenum (Mo): Increasing high-temperature strength and creep resistance.
This combination of elements gives DIN 2714 its unique ability to withstand extreme operating conditions while maintaining dimensional stability.
Key Properties of DIN 2714 Steel
- High Toughness: With its exceptional toughness, DIN 2714 resists cracking and – chipping, even under heavy loads.
- Excellent Thermal Stability: The steel maintains its mechanical properties at elevated temperatures, making it perfect for hot work applications.
- Wear Resistance: The material can endure prolonged exposure to abrasion, increasing the longevity of forging dies and tools.
- Hardenability: DIN 2714 can achieve a consistent hardness profile, ensuring uniform performance across the material.
Applications in the Forging Industry
DIN 2714 steel’s properties make it indispensable in several forging processes. Some of its primary applications include:
- Forging Dies: The wear resistance and toughness of DIN 2714 make it an excellent choice for dies used in drop forging and upset forging.
- Hot Shear Blades: The steel’s ability to maintain hardness at high temperatures is ideal for cutting hot metal billets.
- Extrusion Tools: DIN 2714’s thermal stability and wear resistance are advantageous in metal extrusion processes.
- Press Tools: These tools require materials that can withstand repeated stress and high impact, making DIN 2714 a preferred choice.
Benefits of Using DIN 2714 Steel
- Increased Tool Life: The superior wear resistance and toughness reduce the frequency of tool replacement, cutting down costs and downtime.
- Improved Efficiency: The steel’s thermal stability allows tools to operate efficiently under high temperatures, enhancing production rates.
- Cost-Effectiveness: Although the initial investment may be higher, the extended tool life and reduced maintenance offset the costs, delivering long-term savings.
- Enhanced Performance: Tools made from DIN 2714 ensure precise and high-quality forging results, meeting stringent industrial requirements.
Conclusion
The forging industry demands materials that can withstand extreme conditions while delivering consistent performance. DIN 2714 steel checks all these boxes, making it a preferred material for manufacturing critical forging tools. By choosing DIN 2714, industries can achieve enhanced productivity, reduced operational costs, and superior product quality.
At Virat Special Steels, we are committed to delivering the highest quality DIN 2714 steel tailored to meet the diverse needs of the forging industry. Partner with us to unlock the potential of this exceptional material and elevate your forging operations to new heights.
FAQ: The Role of DIN 2714 Steel in Forging Industries
1. What is DIN 2714 steel?
DIN 2714 is a German-standard hot work tool steel known for its excellent toughness, wear resistance, and thermal stability. It is widely used in the forging industry for its ability to withstand high temperatures and heavy mechanical loads.
2. What are the key components of DIN 2714 steel?
The primary components of DIN 2714 steel include:
- Carbon (C) for hardness and strength.
- Silicon (Si) for heat resistance.
- Manganese (Mn) for toughness and hardenability.
- Chromium (Cr) for corrosion resistance and strength.
- Molybdenum (Mo) for high-temperature strength.
3. Why is DIN 2714 steel preferred in the forging industry?
DIN 2714 steel is preferred due to its combination of high toughness, wear resistance, thermal stability, and hardenability. These properties make it ideal for manufacturing forging dies, hot shear blades, extrusion tools, and press tools.
4. What applications is DIN 2714 steel suitable for?
DIN 2714 steel is commonly used in:
- Forging dies
- Hot shear blades
- Metal extrusion tools
- Press tools for hot work applications
5. What are the benefits of using DIN 2714 steel in forging?
The key benefits include:
- Prolonged tool life due to high wear resistance
- Improved efficiency in high-temperature operations
- Cost-effectiveness through reduced maintenance and downtime
- Consistent and precise forging results
6. How does DIN 2714 compare with other hot work tool steels?
DIN 2714 stands out for its balanced properties, such as toughness, wear resistance, and heat resistance. It offers an optimal combination of durability and performance, making it a reliable choice for heavy-duty forging tools.
7. Can DIN 2714 steel be customized for specific applications?
Yes, DIN 2714 steel can be heat-treated and machined to meet specific requirements of different forging applications. Working with a trusted supplier ensures customization tailored to your operational needs.
8. What is the typical service life of tools made from DIN 2714 steel?
The service life varies based on the application, maintenance practices, and operating conditions. However, DIN 2714’s durability ensures longer tool life compared to many other materials.
9. How should DIN 2714 steel be maintained to maximize its performance?
Proper maintenance includes regular inspection for wear, timely heat treatment, and ensuring that tools operate within their recommended temperature range. This helps in prolonging the tool’s service life.
10. Where can I source high-quality DIN 2714 steel?
Virat Special Steels is a trusted supplier of premium DIN 2714 steel, offering products tailored to the needs of the forging industry. Contact us to learn more about our offerings and how we can support your business.
Mode of Supply:
Virat Special Steels is the largest stockiest and supplier of DIN 2714 tool steel in flat, square and round bar. We provide steel in all sizes as your requirements. DIN 2714 die steel is available in flat, square and round shape.
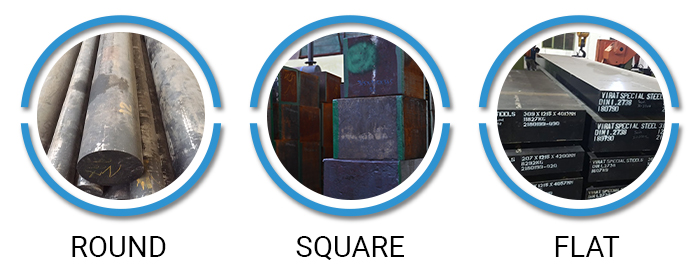
Consult our team who will assist you for DIN 2714 steel query.
https://www.viratsteels.com/din-2714.html
🌐https://www.viratsteels.com 📩info@viratsteels.com 📲+91-98140-21775
Critical Applications of DIN 2344 Steel in the Automotive Industry!
Steel remains the backbone of the automotive industry, providing the strength and resilience required for modern vehicles. Among the various grades of steel used, DIN 2344 steel holds a prominent place due to its exceptional performance under challenging conditions. This article explores the critical applications of DIN 2344 steel in the automotive industry, showcasing why it is a preferred material for manufacturers globally.
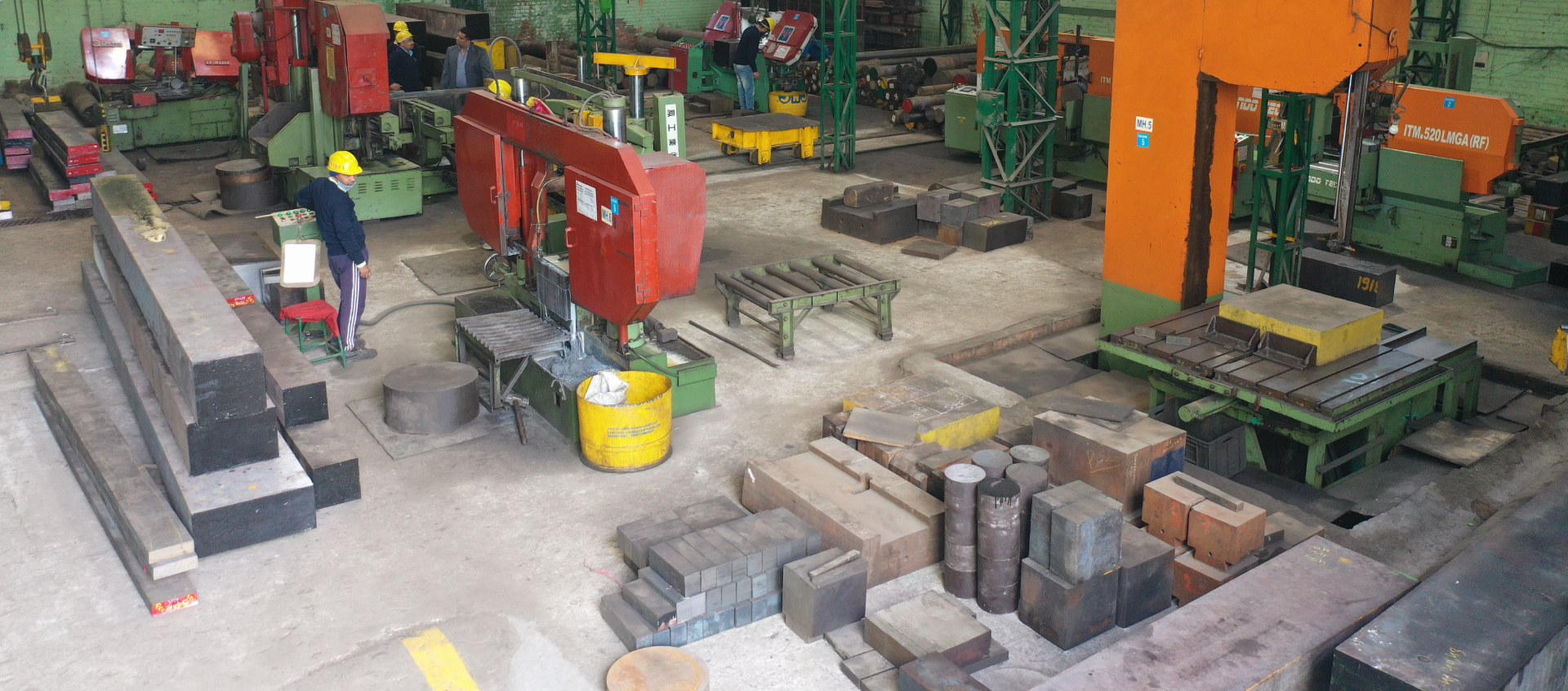
What is DIN 2344 Steel?
DIN 2344 steel, also known as H13 tool steel, is a versatile, high-performance material widely utilized in hot work applications. Classified as a chromium-molybdenum steel alloy, it is specially engineered for superior heat resistance, toughness, and wear properties.
Key Properties of DIN 2344 Steel
- Thermal Resistance: With its ability to retain strength and hardness at elevated temperatures, DIN 2344 is perfect for high-heat environments.
- Toughness and Durability: Its superior toughness makes it resistant to cracking and deformation.
- Corrosion Resistance: With strong resistance against oxidizing environments, it outperforms many other alloys.
- Machinability: While challenging to machine, advanced processes have streamlined its incorporation in various automotive applications.
Importance of DIN 2344 Steel in Modern Industry
The global shift toward lightweight yet robust materials has spotlighted DIN 2344 steel, particularly in automotive manufacturing. With its combination of toughness and flexibility, it meets the demands of advanced production lines.
Relevance of DIN 2344 Steel in Automotive Manufacturing
1. Historical Context of Material Usage in Automotive Engineering
Steel has evolved over decades as the material of choice in automotive engineering. From basic carbon steels to high-alloy steels like DIN 2344, each advancement reflects a need to address emerging challenges, including efficiency, safety, and sustainability.
2. Why DIN 2344 is Perfect for the Automotive Sector?
The automotive industry faces constant pressure to produce durable, efficient, and lightweight vehicles. DIN 2344 steel meets these demands with its remarkable properties, offering enhanced strength for components that endure high-stress conditions.
Applications of DIN 2344 Steel in Automotive Components
- Use in Die Casting Tools: Die casting forms a vital part of automotive manufacturing, especially for producing lightweight engine and body components.
- Significance in Aluminum and Magnesium Alloy Casting. DIN 2344 steel excels in die-casting tools used for aluminum and magnesium alloys, offering superior wear resistance and prolonging tool life in high-temperature operations.
- Molds for Plastic Injection: As plastics gain traction in automotive design, durable molds made from DIN 2344 steel ensure precise shaping of components, contributing to reduced production defects and downtime.
- Hot Forming and Forging Applications: DIN 2344 steel is indispensable in hot forming and forging operations due to its ability to maintain hardness and strength even at elevated temperatures.
- Applications in Exhaust Systems and Engine Components:
- Enhanced Durability in High-Temperature Environments: From turbochargers to exhaust manifolds, DIN 2344 steel ensures resistance to thermal fatigue, ensuring reliability in extreme engine environments.
Benefits of Using DIN 2344 Steel
- High Wear Resistance: The wear resistance of DIN 2344 enhances the lifespan of tools and components, reducing frequent replacements and minimizing downtime.
- Excellent Thermal Stability: DIN 2344 steel maintains its structural integrity under high-temperature operations, a critical advantage for heat-intensive automotive processes.
- Corrosion Resistance: Superior resistance to oxidation and other corrosive agents ensures long-term durability, even under severe operating conditions.
- Cost-Effectiveness in Automotive Production: Reduced downtime, longer tool life, and enhanced product performance result in significant cost savings for manufacturers.
Challenges and Considerations
- Machining and Heat Treatment Challenges: While offering unmatched performance, DIN 2344 steel poses challenges in machining and heat treatment. Manufacturers must employ specialized techniques to overcome these hurdles.
- Alternatives to DIN 2344 Steel: In scenarios where DIN 2344 isn’t suitable, alternatives such as D2 or P20 steels might be considered based on specific application requirements.
Innovations and Future Applications
- Emerging Automotive Trends Impacting Material Choice: Electric vehicles and lightweight design trends are shaping the use of advanced steels, with DIN 2344 continuing to play a pivotal role.
- Future-Ready Technologies Enabled by DIN 2344 Steel: From 3D-printed automotive parts to precision components for EVs, the versatility of DIN 2344 opens pathways for innovative designs.
Sustainability and Environmental Impact
- How DIN 2344 Supports Energy Efficiency: The durability of DIN 2344 reduces waste in production, while its energy-efficient processing ensures environmentally friendly manufacturing practices.
- Recycling and Reusability in the Automotive Supply Chain: DIN 2344 steel components can be recycled and reused, supporting circular economy principles and reducing the industry’s carbon footprint.
Conclusion:
DIN 2344 steel stands as a cornerstone in the automotive industry, enabling the creation of high-performance vehicles and components. With its unique properties and adaptability, it continues to shape the future of manufacturing.
Mode of Supply
Virat Special Steels is the largest stockiest and supplier of DIN 2344 tool steel in flat, square and round bar. We provide steel in all sizes as your requirements. DIN 2344 die steel is available in flat, square and round shape. Consult our team who will assist you for DIN 2344 steel query.
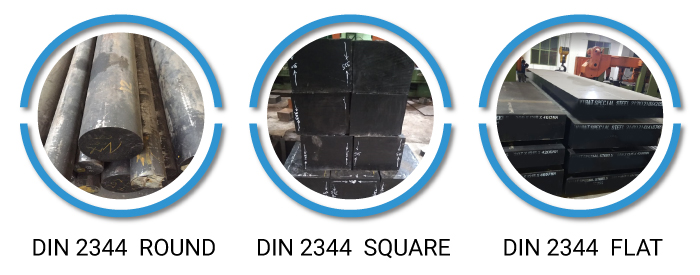
FAQs
- What makes DIN 2344 steel ideal for the automotive industry?
Its exceptional heat resistance, wear resistance, and durability make it indispensable for high-stress applications like die-casting and forging tools. - Can DIN 2344 steel withstand extreme temperatures in engine systems?
Yes, DIN 2344 offers excellent thermal stability and is ideal for components in high-temperature environments, such as exhaust systems. - How does DIN 2344 steel contribute to cost-efficiency in manufacturing?
Its durability and wear resistance minimize tool replacement costs, reducing downtime and production expenses. - Are there eco-friendly aspects to using DIN 2344 steel in automotive production?
Yes, its recyclability and reduced waste in the production process support sustainable manufacturing practices. - What are the alternatives if DIN 2344 steel isn’t viable?
D2 or P20 steels are viable alternatives, depending on application needs and operating conditions.
Exploring DIN 2714, A Comprehensive Guide
In the industrial world, the type of steel used often defines the success of an operation. With industries increasingly relying on robust and versatile materials, steel grades like DIN 2714 have gained tremendous importance. DIN 2714 is a tool steel renowned for its exceptional mechanical properties and versatile applications. It serves as a pivotal element in numerous industrial domains, driving innovation and efficiency.
This comprehensive guide explores the composition, characteristics, and applications of DIN 2714, shedding light on why this particular steel grade is vital for modern manufacturing.
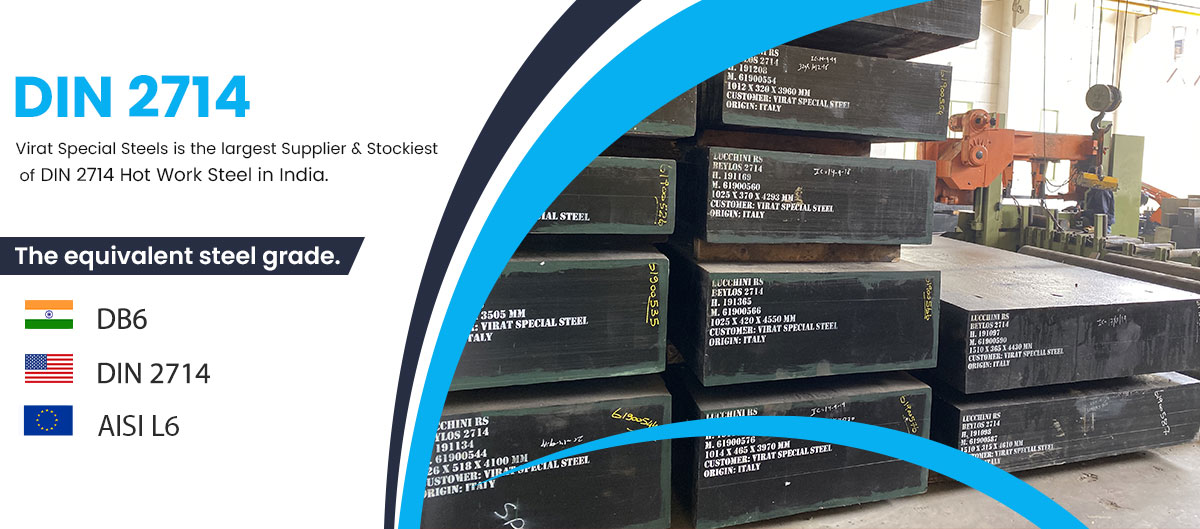
Understanding DIN 2714 Steel
DIN 2714 is classified as a hot-working tool steel, primarily known for its exceptional resistance to deformation at high temperatures. Developed in compliance with the German industrial standard, this steel stands out for its adaptability, toughness, and wear resistance, making it a favored choice for die-making industries.
Historically, the development of DIN 2714 was driven by the need for a material that could withstand extreme stress without compromising on durability. Today, it has become synonymous with reliability and performance in demanding applications.
Chemical Composition of DIN 2714
The chemical makeup of DIN 2714 significantly influences its characteristics. The main components include:
- Carbon (C): Around 0.50% to enhance hardness and strength
- Chromium (Cr): Approx. 1.2% to 2.0%, imparting wear resistance
- Manganese (Mn): Between 0.70% to 1.0%, aiding in toughness
- Silicon (Si): 0.25% to 0.40% for improved machinability
- Molybdenum (Mo): Around 0.30%, increasing high-temperature strength
- Vanadium (V): Small quantities for grain refinement
This precise composition ensures optimal mechanical properties, including high tensile strength, toughness, and durability under extreme conditions.
Physical Properties of DIN 2714 Steel
What makes DIN 2714 stand apart? Here are its key physical properties:
- Hardness: Exceptional durability ensures long-lasting performance even in abrasive conditions.
- Tensile Strength: DIN 2714 boasts a tensile strength of over 1,100 MPa, making it ideal for heavy-duty applications.
- Density: Approximately 7.85 g/cm³, offering a perfect balance of weight and toughness.
These attributes make it suitable for applications involving high pressures and temperatures, ensuring long operational lifespans.
Key Characteristics of DIN 2714
DIN 2714’s features extend beyond its composition.
- Heat Resistance: Its ability to endure high temperatures makes it ideal for hot-working environments.
- Machinability: With excellent machinability, manufacturers can shape this steel with precision, minimizing processing time.
- Weldability: Smooth weldability ensures easy integration into larger assemblies, reducing operational costs.
- Corrosion Resistance: While not highly corrosion-resistant, its treatment processes often include anti-corrosion coatings.
Common Applications of DIN 2714 Steel
DIN 2714 is used across various industries due to its versatility:
- Tool Manufacturing: Ideal for making heavy-duty forging dies, cutting tools, and machine components.
- Industrial Machinery: Widely used in presses, punches, and molds where precision and durability are critical.
- Aerospace and Automotive: Suited for high-stress components like gears and crankshafts due to its toughness.
Heat Treatment Process of DIN 2714 Steel
The heat treatment process significantly enhances the performance and durability of DIN 2714 steel, making it more suited for demanding applications. Let’s break down the stages involved:
- Annealing:
This process softens the steel to make it easier to machine. DIN 2714 steel is typically heated to a range of 820°C to 860°C and then cooled gradually in a furnace. - Hardening:
For increased strength, the steel is heated to a higher temperature range, typically between 1,020°C and 1,050°C, and then quenched in oil or water. - Tempering:
After quenching, the steel becomes brittle. Tempering at temperatures between 550°C and 650°C reduces brittleness while retaining hardness, enhancing its toughness. - Stress Relieving:
To eliminate residual stresses, DIN 2714 is reheated to approximately 600°C, maintaining structural stability during use.
The heat treatment process ensures DIN 2714 performs optimally in hot and high-pressure applications.
Comparison with Other Steel Grades
Understanding how DIN 2714 stacks up against other steel grades offers perspective on its unique benefits:
- DIN 2714 vs. EN 24 Steel:
While EN 24 is a popular alloy steel with excellent strength, DIN 2714 excels in high-temperature applications due to its superior heat resistance. - DIN 2714 vs. DIN 17350:
DIN 17350, though robust, lacks the enhanced machinability and resistance properties of DIN 2714, making it less versatile for hot-working environments.
DIN 2714 provides a balanced combination of toughness, resistance, and machinability unmatched by its counterparts.
Benefits of Using DIN 2714
DIN 2714 has numerous advantages that make it a go-to choice for industries:
- Cost-Effectiveness: Despite its premium properties, it’s reasonably priced compared to other high-performance steels.
- Versatility: Its wide range of applications, from tooling to machinery parts, highlights its adaptability.
- Durability: High resistance to wear and tear ensures fewer replacements and repairs over time, saving costs.
These benefits combine to make DIN 2714 a practical choice for manufacturers across industries.
Limitations and Challenges
Even the best materials have their limitations, and DIN 2714 is no exception:
- Limited Corrosion Resistance: While its wear and heat resistance is impressive, DIN 2714 requires proper coatings or treatments to prevent corrosion in moisture-prone environments.
- Specialized Handling: The heat treatment process demands expertise, which can increase production costs for inexperienced manufacturers.
- Specific Use Cases: Though versatile, its applications are often limited to specific industrial domains like tooling and heavy machinery.
These challenges necessitate careful planning when opting for DIN 2714 steel.
Specifications and Standards of DIN 2714
DIN 2714 complies with stringent standards, ensuring its reliability and quality:
- Chemical Composition: Strictly regulated to ensure consistent mechanical and thermal properties.
- Dimensional Standards: Meets ISO tolerances for precision in industrial applications.
- Testing Requirements: Regular quality control through tensile, hardness, and impact tests guarantees its performance under stress.
This level of compliance makes DIN 2714 a globally trusted steel grade.
Factors to Consider When Choosing DIN 2714 Steel
Selecting DIN 2714 for a specific application involves analyzing several factors:
- Application Suitability: Ensure it aligns with the demands of the job, such as high-temperature operations or heavy loads.
- Budget: While cost-effective in the long run, initial investment considerations remain essential.
- Maintenance Requirements: Plan for potential treatments or coatings to enhance durability and prevent corrosion.
By understanding these factors, manufacturers can maximize the value of using DIN 2714.
Market Demand for DIN 2714 Steel
As industries expand, the demand for reliable materials like DIN 2714 grows:
- Global Trends: Rapid industrialization in Asia and technological advancements in Europe are key drivers.
- Industry-Specific Needs: Rising reliance on automation and high-performance machinery further fuels demand.
Geographically, countries like Germany, China, and the USA lead in importing and using DIN 2714 steel, reflecting its global significance.
Sustainability and Environmental Considerations
In today’s eco-conscious world, DIN 2714’s recyclability makes it a preferred choice:
- Recycling Potential: Steel is one of the most recycled materials globally, contributing to reduced environmental impact.
- Waste Reduction: Longer lifespans mean less frequent replacements, minimizing industrial waste.
- Energy Efficiency: Advanced production techniques reduce energy consumption, making DIN 2714 an environmentally friendly option.
Adopting DIN 2714 aligns with green manufacturing goals while maintaining industrial efficiency.
Conclusion
DIN 2714 stands as a testament to innovation in the steel industry. Its unique blend of toughness, heat resistance, and machinability makes it indispensable for applications that demand durability under extreme conditions. Though it comes with challenges, its benefits far outweigh them, ensuring its place in the toolbox of manufacturers worldwide.
By understanding its properties, treatment processes, and applications, industries can fully harness the potential of DIN 2714, driving efficiency and excellence.
Mode of Supply
Virat Special Steels is the largest stockiest and supplier of DIN 2714 tool steel in flat, square and round bar. We provide steel in all sizes as your requirements. DIN 2714 die steel is available in flat, square and round shape. Consult our team who will assist you for DIN 2714 steel query.
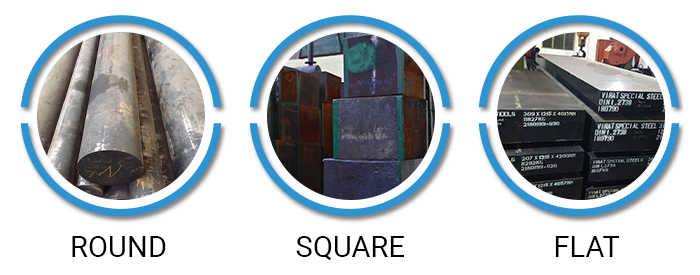
FAQs
- What is the primary use of DIN 2714 steel?
DIN 2714 is primarily used in tool manufacturing, particularly for forging dies and heavy-duty cutting tools. - Can DIN 2714 steel resist corrosion?
It has limited corrosion resistance and typically requires coatings or treatment for moisture-heavy environments. - How does DIN 2714 compare to other tool steels?
DIN 2714 offers superior heat resistance and machinability compared to most other tool steels, making it ideal for high-temperature applications. - What industries benefit most from DIN 2714?
Industries like automotive, aerospace, and heavy machinery manufacturing frequently use DIN 2714 for critical components. - Is DIN 2714 eco-friendly?
Yes, its recyclability and durability contribute to reducing industrial waste, making it an environmentally friendly choice.
Comparing DB6 Steel vs H13 Steel: Key Differences and Uses
In the world of tool steels, DB6 and H13 stand out as two popular choices. Known for their reliability and performance, these steels serve a variety of industries such as automotive, aerospace, and die-making. But how do these two materials compare, and what are their most suitable applications?
Let’s dive deep into their properties, differences, and uses to help you make an informed decision.
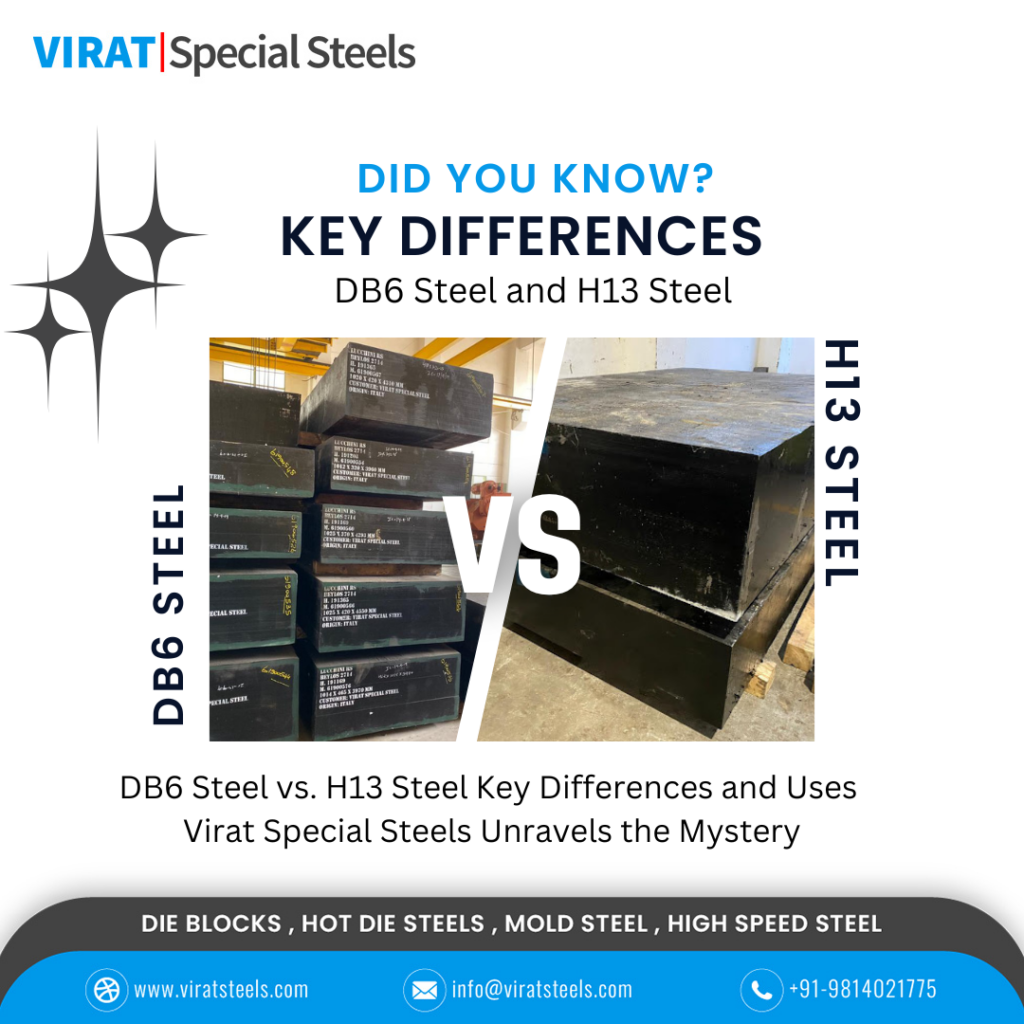
1. Understanding DB6 Steel
DB6 steel, or D6 steel, is a high-carbon, high-chromium tool steel. It boasts impressive wear resistance and is often utilized in applications requiring durability and hardness.
Key Properties of DB6 Steel
- High Hardness: DB6 excels in maintaining high hardness even under stress.
- Abrasion Resistance: Its chromium-rich composition offers superb abrasion resistance, making it ideal for demanding environments.
- Dimensional Stability: It resists deformation under heat and mechanical pressure.
Applications of DB6 Steel
DB6 steel is primarily used in:
- Cold-working applications like die casting molds
- Punches and cutting tools
- Deep-drawing dies
It is a go-to choice for processes requiring precision and wear resistance.
2. Understanding H13 Steel
H13 steel is a chromium-molybdenum alloy with exceptional toughness and versatility. It performs well across a wide temperature range, making it an industry favorite.
Key Properties of H13 Steel
- High Thermal Strength: H13 retains its mechanical strength even at elevated temperatures.
- Shock Resistance: Excellent impact resistance makes it ideal for heavy-duty applications.
- Versatility: Suitable for both hot-working and cold-working processes.
Applications of H13 Steel
Commonly, H13 steel is used in:
- Injection molding dies
- Hot forging dies
- Aerospace and automotive components
Its versatility makes it indispensable for industries where temperature changes are a factor.
3. Composition Comparison: DB6 vs. H13
Understanding the chemical composition of both steels is crucial for identifying their potential use cases.
Element | DB6 Steel | H13 Steel |
Chromium | High (12%–14%) | Moderate (4.75%–5.50%) |
Carbon | High (1.4%–1.6%) | Lower (0.32%–0.45%) |
Molybdenum | Low | High (1.2%–1.5%) |
Vanadium | Trace | Present (0.8%–1.2%) |
Silicon | Moderate (0.4%–0.7%) | Low (0.8%–1.0%) |
The higher chromium content in DB6 gives it better wear resistance, while the molybdenum in H13 offers enhanced thermal stability and toughness.
4. Mechanical Properties Comparison
Property | DB6 Steel | H13 Steel |
Hardness | Extremely high | High |
Thermal Resistance | Moderate | Excellent |
Wear Resistance | Superior | Good |
Toughness | Moderate | Superior |
DB6 excels in situations demanding high wear resistance and hardness, while H13’s toughness makes it better suited for impact-heavy and high-heat applications.
5. Key Differences Between DB6 and H13 Steel
Feature | DB6 Steel | H13 Steel |
Best for | Cold-working applications | Hot-working and high-impact jobs |
Thermal Capability | Limited | Suitable for high temperatures |
Impact Resistance | Lower | Higher |
Corrosion Resistance | High | Moderate |
These differences highlight how each steel caters to specific industrial needs.
6. Choosing the Right Steel: DB6 vs. H13
When deciding between DB6 and H13, consider:
- Work Conditions: Is the application exposed to high temperatures or high wear?
- Desired Properties: Do you need exceptional wear resistance (DB6) or superior toughness (H13)?
- Budget: H13 is generally more cost-effective for its versatility, but DB6 offers long-term durability.
7. Common Industries and Their Preference
Industry | Preferred Steel | Reason |
Tool & Die Making | DB6 Steel | Excellent wear resistance for extended tool life. |
Automotive | H13 Steel | Handles the heat and stress of forging components. |
Aerospace | H13 Steel | Resilient to thermal fatigue in extreme environments. |
8. Cost Implications
- DB6 Steel: Higher cost due to chromium and specialized applications.
- H13 Steel: More affordable, widely available, and multi-functional.
9. Maintenance and Longevity
Proper care ensures both steels perform optimally.
- DB6: Periodic inspection for cracks and maintaining cool temperatures can extend its lifespan.
- H13: Regular thermal treatments enhance its resilience against wear and fatigue.
10. Final Verdict
Both DB6 and H13 steels have their strengths. While DB6’s wear resistance makes it unbeatable for cold applications, H13’s versatility shines in demanding thermal environments. The final choice depends on your project’s specific requirements.
Conclusion
Choosing between DB6 and H13 steel isn’t a one-size-fits-all decision. By understanding their unique properties and applications, you can match the steel to your manufacturing needs effectively. Whether it’s the durability of DB6 or the robustness of H13, both steels promise performance when used in the right setting.
FAQs
- What makes H13 suitable for hot applications?
H13’s composition with molybdenum and vanadium gives it superior thermal stability and resistance to heat deformation. - Is DB6 more expensive than H13?
Yes, DB6 typically costs more due to its specialized high-chromium content and niche applications. - Can H13 steel be used for cold applications?
Yes, but DB6 steel is better for cold applications due to its higher wear resistance. - Which steel offers better impact resistance?
H13 steel is superior in impact resistance, thanks to its toughness and balanced alloy composition. - How can I maintain DB6 steel?
Regular inspections for wear and avoiding prolonged exposure to high temperatures can maximize DB6’s lifespan.
What Is DB6 Steel? Key Properties and Industrial Applications
DB6 steel, a versatile and high-performance tool steel, has emerged as a preferred choice for industries requiring durability, strength, and precision. Classified under high-strength, high-alloy steels, DB6 is specifically engineered to withstand mechanical stress and challenging working conditions, making it indispensable in sectors like automotive, aerospace, and tool manufacturing.
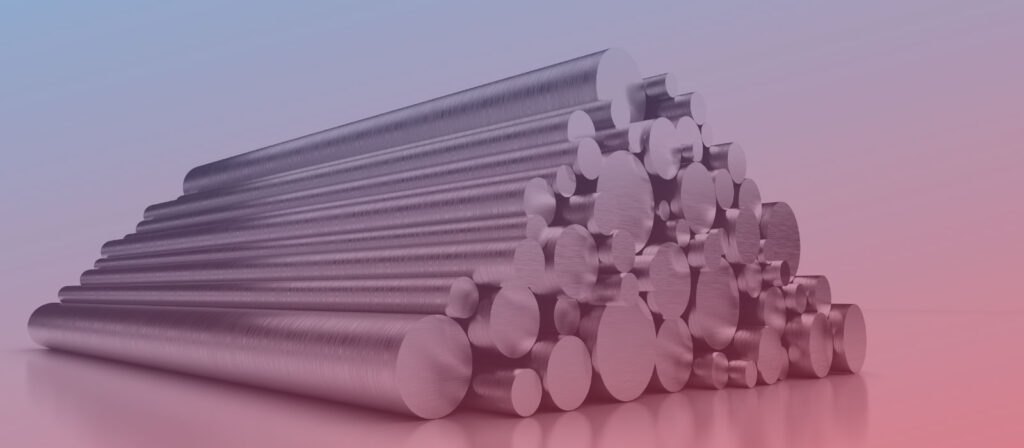
Historically developed as an upgrade to standard tool steels, DB6 has garnered a reputation for its superior hardness and excellent wear resistance. Whether you’re shaping industrial tools or crafting high-stress components, this material delivers consistent results. Its robustness and adaptability make it a prime candidate for modern-day manufacturing challenges.
Composition of DB6 Steel
The composition of DB6 steel is what sets it apart, combining a precise mix of elements to achieve unmatched properties. Some key constituents include:
- Carbon (C): Enhances hardness and strength.
- Chromium (Cr): Improves corrosion resistance and wear resistance.
- Molybdenum (Mo): Contributes to thermal stability and tensile strength.
- Vanadium (V): Adds resistance to abrasion and shock.
- Nickel (Ni): Provides toughness and improves machinability.
Each of these elements plays a pivotal role in shaping the material’s performance, ensuring that DB6 steel stands up to even the most demanding industrial environments.
Key Properties of DB6 Steel
Mechanical Strength and Hardness
One of the standout characteristics of DB6 steel is its extraordinary mechanical strength. It boasts impressive tensile strength, making it suitable for high-pressure applications. Its inherent hardness ensures excellent wear resistance, extending the longevity of tools and components.
Thermal Stability
DB6 steel can retain its properties under high temperatures, making it an ideal choice for thermal-intensive applications. From furnace tools to automotive parts operating in heated environments, it stays reliable and effective.
Corrosion Resistance
Unlike ordinary steels, DB6 is fortified against rust and corrosion. The presence of chromium acts as a protective shield, allowing it to perform efficiently even in corrosive environments.
Machinability and Weldability
Despite its hardness, DB6 steel offers good machinability when worked with modern tools. Its weldability makes it a practical choice for projects requiring intricate assembly.
Types of DB6 Steel Treatments
To optimize its performance, DB6 steel can undergo various treatments. Here’s a breakdown:
Heat Treatment
Heat treatment alters the microstructure, increasing its toughness and mechanical resilience. This makes DB6 ideal for use in tools that require precision under stress.
Surface Hardening
Through methods like carburizing and nitriding, the surface of DB6 can be hardened while retaining a soft core, ensuring better impact resistance.
Annealing
Annealing softens DB6 steel, improving its machinability and making it easier to work into specific shapes before hardening.
Industrial Applications of DB6 Steel
Tool and Die Manufacturing
DB6 is a cornerstone in tool and die manufacturing due to its high durability and resistance to deformation. Molds, dies, and cutting tools crafted from DB6 perform exceptionally well under repeated use.
Automotive Sector
From crankshafts to heavy-duty gears, DB6 steel finds widespread use in automotive parts that endure high stress, ensuring safety and longevity.
Aerospace Engineering
The aerospace sector demands precision and resilience. DB6 steel is used in high-stress areas such as landing gears and turbine components.
Construction and Heavy Equipment
For applications like hydraulic presses and structural bearings, DB6 steel offers the perfect mix of toughness and flexibility, keeping large structures secure and functional.
Why Choose Virat Special Steels for Your DB6 Steel Needs?
When it comes to sourcing premium-quality DB6 steel, Virat Special Steels is a name you can trust. With years of expertise in manufacturing and distribution, the company delivers steels that meet international standards and specific project requirements.
Why us?
- We maintaining a high level of inventory from world-renowned manufacturers such as Swiss Steel Group (DEW), Nippon Koshuha Steels Co. Ltd, Hyundai Steel, SeAH Besteel Corp and many more.
- We ensure rigorous quality checks.
- Competitive pricing without compromising on performance.
- Dedicated customer support and on-time delivery.
Choose VIRAT SPECIAL STEELS for a seamless blend of quality, variety, and reliability in every steel grade.
Contact us today to buy the best quality DB6 / DIN 2714 steel for your tooling needs! https://www.viratsteels.com/db6.html / https://www.viratsteels.com/din-2714.html
Any further queries feel free to contact us :
🌐https://www.viratsteels.com 📩info@viratsteels.com 📲+91-98140-21775
H13 Tool Steel Hardness: Methods to Test and Optimize Performance
Introduction
H13 tool steel stands out for its remarkable durability and thermal resistance, making it a preferred choice in industries such as automotive, aerospace, and manufacturing. However, its effectiveness hinges on maintaining optimal hardness, which directly impacts wear resistance, toughness, and performance under stress. This article explores various methods for testing H13 steel hardness and strategies to optimize it for maximum utility.
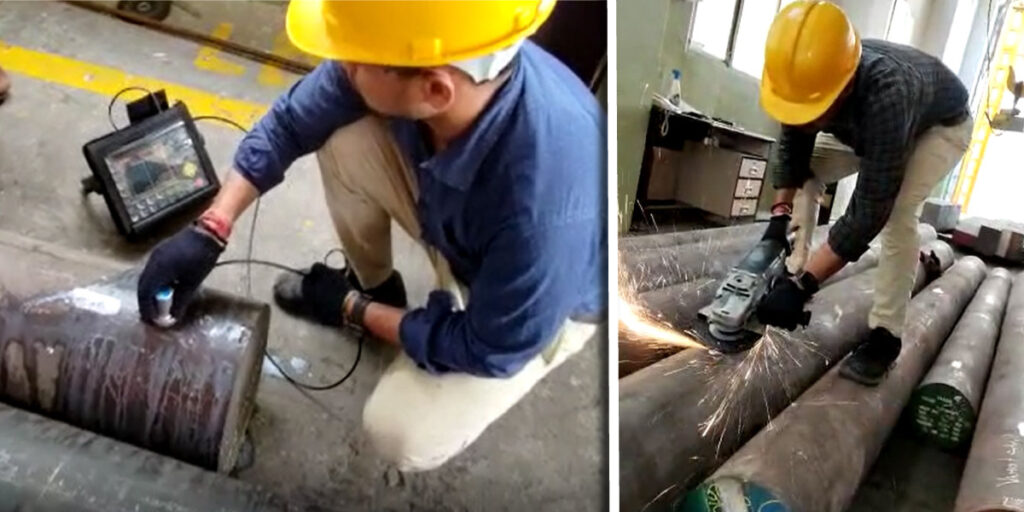
What is H13 Tool Steel?
H13 is a chromium-molybdenum hot work tool steel renowned for its exceptional strength and heat resistance. It contains:
- Chromium for enhanced corrosion resistance.
- Molybdenum and vanadium for superior toughness and wear resistance.
H13’s properties make it ideal for applications like:
- Forging dies.
- Injection molding tools.
- Extrusion dies.
- Die-casting components.
This robust tool steel withstands thermal fatigue, making it invaluable in environments with rapid temperature fluctuations.
Read More >What Industries Benefit the Most from Using H13 Steel?
Introduction
In the vast world of industrial materials, few tool steels have made as significant an impact as H13 steel. Renowned for its exceptional durability, heat resistance, and machinability, H13 steel stands as a cornerstone in industries requiring high-performance materials. From automotive manufacturing to plastic molding, this versatile steel helps businesses thrive by enhancing productivity and ensuring long-term efficiency.
Whether you’re an industry expert or a curious reader, understanding the benefits and applications of H13 steel sheds light on why it is so widely celebrated. Let’s explore what makes H13 steel an indispensable choice for various industries.
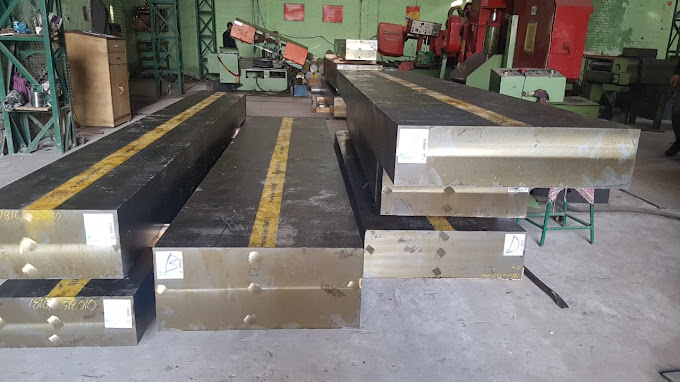
Understanding H13 Steel
What Is H13 Steel?
H13 steel is a chromium-molybdenum hot-work tool steel that offers exceptional strength and resistance to thermal fatigue. Classified as an H-grade steel, it is specially engineered for high-temperature applications. Its unique composition includes:
- Carbon: Provides hardness.
- Chromium and Molybdenum: Enhance toughness and heat resistance.
- Vanadium: Adds wear resistance.
Unique Characteristics of H13 Steel
H13 steel’s distinguishing properties make it one of the most trusted materials for heavy-duty industrial purposes:
- High thermal stability and resistance to cracking under thermal cycling.
- Exceptional machinability and ease of finishing.
- Outstanding toughness and abrasion resistance.
Common Applications in Industry
From manufacturing molds to constructing durable tools, H13 steel has applications across various demanding environments. It’s especially suited for high-heat tasks, such as die-casting and injection molding.
The Importance of H13 Steel in Industrial Sectors
In today’s competitive market, industries are constantly on the lookout for materials that can endure intense conditions without compromising efficiency. H13 steel has earned a reputation for its ability to reduce downtime and extend the lifespan of tools. Its versatility and reliability allow companies to deliver products that meet rigorous performance standards.
Industries That Benefit the Most from H13 Steel
Automotive Industry
The automotive sector thrives on precision and durability, and H13 steel plays an integral role in achieving these goals. The material’s heat resistance and toughness make it a prime choice for:
- Die-casting molds: Creating engine parts and automotive components.
- High-temperature tools: Handling demanding manufacturing processes without deforming or cracking.
Aerospace Industry
Aviation demands high precision and reliability. H13 steel contributes to the aerospace industry by being an ideal material for:
- Forging dies and cutting tools.
- Heat-treated aviation components that endure extreme stress and temperature changes.
Plastic Molding and Manufacturing
In the realm of plastic production, injection molds are under constant pressure to perform efficiently. H13 steel ensures the longevity and quality of:
- Injection molds: That shape plastics for consumer goods.
- Tooling parts: That resist wear from continuous production cycles.
Die-Casting Industry
The die-casting sector relies heavily on H13 steel for its ability to withstand molten metals. It’s an essential material for:
- High-performance casting molds for aluminum, zinc, and magnesium.
- Precision tools that resist thermal cycling and erosion.
Construction and Heavy Equipment
Heavy industries demand tools and parts that endure tremendous mechanical stress. H13 steel finds its place in:
- Specialized construction machinery parts.
- Tools used in mining and heavy lifting.
Benefits of Using H13 Steel for These Industries
- High Heat Resistance: Maintains its shape and properties under extreme temperatures.
- Durability and Toughness: Resists deformation and cracking under heavy loads.
- Cost Efficiency: Reduces tool replacements and downtime, saving companies money in the long run.
Challenges in Using H13 Steel
Like all materials, H13 steel has challenges:
- Machining Difficulties: Requires skilled handling for optimal results.
- Heat Treatment Needs: Proper treatment is necessary to ensure performance.
- Cost Considerations: While initial costs are high, long-term savings often outweigh this drawback.
Tips for Selecting and Maintaining H13 Steel
- Choose Trusted Suppliers: Ensure quality by sourcing H13 steel from reliable manufacturers like Virat Special Steels.
- Prioritize Heat Treatment: Proper treatment enhances longevity and performance.
- Regular Maintenance: Periodically inspect tools and parts to ensure optimal operation.
Virat Special Steels: A Leader in H13 Steel Supplies
Virat Special Steels is a renowned name in delivering high-quality tool steels, including H13. With decades of industry expertise, Virat has built a reputation for reliability and superior service. Industries across automotive, aerospace, and plastic molding trust Virat for their steel requirements.
Future Trends and Applications of H13 Steel
Advancements in technology continue to unlock new applications for H13 steel, from cutting-edge aerospace innovations to enhanced 3D printing tools. As industries demand more from their materials, H13 steel is expected to remain a cornerstone of industrial growth.
Conclusion
H13 steel is a true industrial powerhouse, serving as a backbone for industries requiring unmatched durability and heat resistance. Its applications across automotive, aerospace, die-casting, and more make it indispensable in achieving quality and performance. For businesses looking to enhance their productivity, H13 steel, supplied by trusted names like Virat Special Steels, remains a wise investment.
FAQs
1. What sets H13 steel apart from other tool steels?
H13 steel offers unmatched heat resistance and durability, making it ideal for high-temperature and high-stress applications.
2. How does H13 steel contribute to cost savings in industries?
Its long lifespan reduces the need for frequent replacements, saving money over time.
3. Can H13 steel be recycled for industrial use?
Yes, H13 steel is recyclable, contributing to sustainable industrial practices.
4. What types of maintenance are needed for H13 steel tools?
Regular inspections, timely heat treatments, and cleaning to avoid contamination can ensure prolonged efficiency.
5. Where can industries procure high-quality H13 steel?
Reliable suppliers like Virat Special Steels specialize in delivering premium-grade H13 steel for diverse industrial needs.
Virat Special Steels is the largest Supplier & Stockiest of H13 Steel in India. Consult our team who will assist you for H-13/ DIN 2344 / AISI H13 steel query. https://www.viratsteels.com/h13.html
Size Range in Forged / Rolled Bars:
Rounds: 13mm Dia to 1500mm Dia
Rectangular: Thickness 13mm – 500mm / Width 13mm to 1500mm
For more information or to discuss your steel needs, Virat Special Steels invites you to reach out through their contact details provided, ensuring a professional and informative experience.
Any further queries feel free to contact us :
🌐https://www.viratsteel.in 📬 info@viratsteels.com ☎+91 98140-21775
Exploring Key Factors for Selecting H13 Steel for Die Applications!
Selecting the right H13 hot work tool steel for die applications involves understanding its properties, assessing your operational requirements, and choosing a reliable supplier. Its unmatched combination of toughness, thermal resistance, and durability makes it an indispensable material for demanding applications. By following the guidelines outlined in this article, you can make an informed decision that ensures optimal die performance and cost-effectiveness.
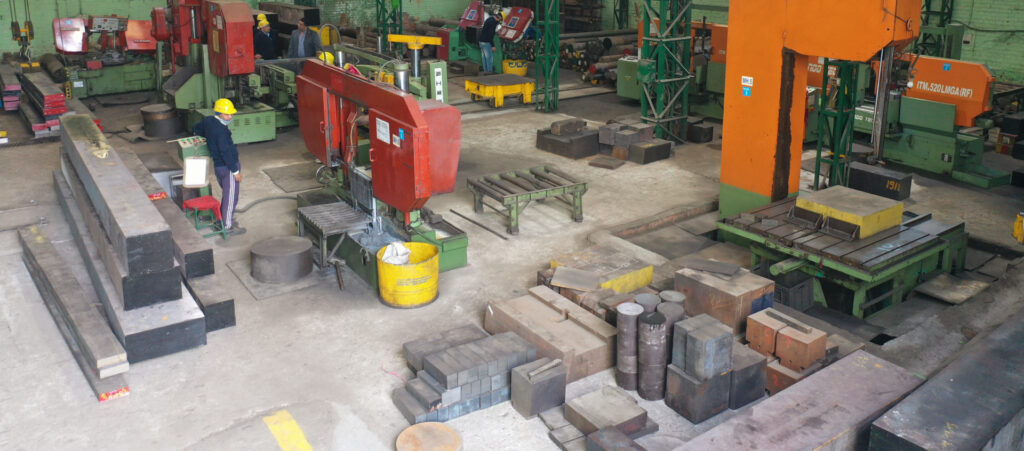
Choosing the right steel for die-making is like laying a solid foundation for a building. It’s the cornerstone that ensures durability, efficiency, and precision in manufacturing processes. Among the wide range of tool steels, H13 hot work tool steel stands out as a preferred choice for die applications. Why? Its excellent combination of toughness, temperature resistance, and durability makes it a favorite across various industries, from automotive to aerospace.
In this guide, we’ll explore everything you need to know about selecting H13 hot work tool steel for your die applications, including what makes it unique and the key factors to consider.
Understanding H13 Hot Work Tool Steel
What is H13 Steel?
H13 is a chromium-molybdenum-vanadium alloy steel, classified as a hot work tool steel. It is specially designed to endure high temperatures, resist thermal fatigue, and maintain structural integrity even under demanding conditions.
Key Properties of H13 Steel
- High Thermal Resistance: Withstands extreme heat without losing strength.
- Toughness and Durability: Handles impact and wear during heavy-duty operations.
- Thermal Conductivity: Promotes effective heat dissipation, preventing die failure.
- Wear Resistance: Resists abrasion and erosion, extending die life.
Advantages of H13 for Die Applications
H13’s balance of strength, hardness, and temperature resistance makes it ideal for hot-working operations such as forging, extrusion, and die-casting. It ensures fewer downtimes, consistent production quality, and reduced replacement costs.
Key Factors to Consider When Selecting H13 Steel for Die Applications
Temperature Resistance
The performance of dies often depends on their ability to handle extreme operating temperatures. H13 steel excels in environments where tools are exposed to temperatures up to 600°C (1112°F) or higher. Industries such as die-casting and forging heavily rely on H13 for its capacity to endure thermal cycling without cracking or deforming.
Hardness and Strength
Hardness directly influences a die’s wear resistance and operational life. H13 steel offers a Rockwell hardness range of 48-54 HRC, making it suitable for heavy-load applications. A well-balanced hardness ensures that the die can withstand repeated impacts and prolonged usage without succumbing to premature wear.
Thermal Conductivity
Heat buildup in dies can lead to dimensional changes, premature wear, and reduced production efficiency. H13’s excellent thermal conductivity ensures uniform heat distribution, which not only protects the die but also enhances the quality of the output by reducing imperfections in the finished product.
Toughness and Impact Resistance
Dies often face high pressure and sudden impacts during operations. H13 steel’s inherent toughness and impact resistance make it capable of absorbing shocks without cracking. This property is especially critical for industries such as automotive manufacturing, where precision and reliability are paramount.
Pre-Treatment and Heat Treatment of H13 Steel
The performance of H13 steel depends significantly on proper pre-treatment and heat treatment. Pre-treatment involves processes like annealing, which enhances machinability. Heat treatment, on the other hand, optimizes hardness, strength, and thermal resistance. Key heat treatment steps include hardening, tempering, and stress relieving, all tailored to the die’s intended application.
Evaluating Quality Standards for H13 Steel
To ensure you’re investing in high-quality H13 steel, look for certifications like ASTM A681 or DIN 1.2344. Premium-grade H13 steel should exhibit uniform composition, minimal impurities, and consistent mechanical properties. It’s advisable to work with reputable suppliers who provide material test certificates (MTC) to guarantee quality.
Applications of H13 Hot Work Tool Steel in Die-Making
H13 steel is used across a broad range of die-making applications, including:
- Die-Casting Dies: Withstands molten metal temperatures and repetitive cooling cycles.
- Forging Dies: Handles high-impact loads without deforming.
- Extrusion Dies: Provides excellent resistance to thermal wear and pressure.
Tips for Purchasing H13 Steel
When buying H13 steel, consider these tips:
- Source from trusted suppliers like Virat Special Steels for consistent quality.
- Verify certifications and specifications.
- Request samples or small batches for testing before large-scale purchase.
Maintenance of H13 Steel Dies
Regular maintenance can significantly extend the life of H13 steel dies. Periodic inspections help identify early signs of wear, such as cracking or pitting. Implementing proper cooling cycles and using lubricants can further enhance the die’s performance and longevity.
FAQs
- What makes H13 steel unique for die-making?
Its exceptional balance of toughness, thermal resistance, and wear resistance. - How does heat treatment impact H13 steel performance?
Heat treatment optimizes hardness and toughness, enhancing durability. - What industries benefit the most from using H13 steel?
Industries like die-casting, forging, and extrusion heavily rely on H13 steel. - How to identify high-quality H13 steel suppliers?
Look for certifications, test reports, and a proven track record of reliability. - What are the common challenges when using H13 dies?
Issues like thermal fatigue and cracking can arise if not properly maintained.
Mode of Supply:
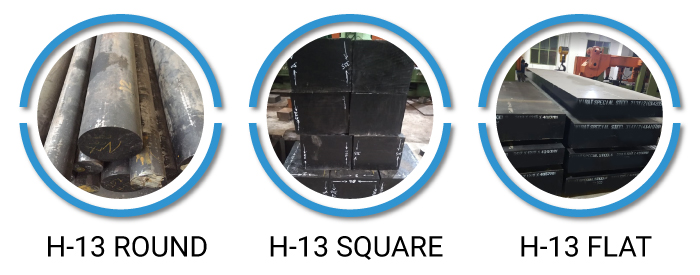
Virat Special Steels is the largest Supplier & Stockiest of H13 Steel in India. Consult our team who will assist you for H-13/ DIN 2344 / AISI H13 steel query. https://www.viratsteels.com/h13.html
Size Range in Forged / Rolled Bars:
Rounds: 13mm Dia to 1500mm Dia
Rectangular: Thickness 13mm – 500mm / Width 13mm to 1500mm
For more information or to discuss your steel needs, Virat Special Steels invites you to reach out through their contact details provided, ensuring a professional and informative experience.
Any further queries feel free to contact us :
🌐https://www.viratsteel.in 📬 info@viratsteels.com ☎+91 98140-21775
DB6 vs High Carbon Steels
When it comes to choosing steel for industrial, tooling, or manufacturing purposes, the choice often boils down to the material’s performance, strength, and durability. DB6 steel and high carbon steels are two prominent contenders in various industries. Each has its unique properties, uses, and advantages.
In this article, we’ll break down the differences between DB6 and high carbon steels to help you make the right decision based on your specific needs.

What is DB6 Steel?
Definition and Composition of DB6 Steel
DB6 is a premium-grade, hot-work tool steel that is specifically designed for die and tooling applications. It belongs to the H-series of tool steels and typically contains chromium, molybdenum, and vanadium as its core alloying elements.
Key Properties of DB6 Steel
- Toughness: DB6 exhibits excellent toughness, which helps it resist cracking under high stress.
- Heat Resistance: It maintains its strength at elevated temperatures.
- Wear Resistance: Due to its alloying elements, DB6 resists wear, making it perfect for heavy-use industrial tools.
- Hardness: It strikes a balance between hardness and machinability.
Common Applications of DB6 Steel
- Die Casting Dies: DB6 is frequently used in aluminum and zinc die-casting dies.
- Extrusion Tools: It excels in hot extrusion applications where heat resistance is critical.
- Plastic Molding: DB6 is utilized for injection molding applications due to its durability.
What are High Carbon Steels?
Definition and Composition of High Carbon Steels
High carbon steels are steels with a carbon content between 0.6% and 1.0%, which gives them enhanced hardness and strength compared to low and medium carbon steels.
Key Properties of High Carbon Steels
- Hardness: High carbon steels achieve high hardness levels when properly heat-treated.
- Strength: Their higher carbon content contributes to excellent tensile strength.
- Wear Resistance: High carbon steels resist abrasion effectively in moderate conditions.
- Machinability: They are harder to machine compared to low carbon steels but can be shaped under specific conditions.
Common Applications of High Carbon Steels
- Cutting Tools: Knives, blades, and cutting tools often rely on high carbon steels.
- Springs: Due to their elasticity and strength, high carbon steels are widely used for springs.
- Wires and Cables: Strong wires are frequently made using high carbon steels.
DB6 vs. High Carbon Steels: A Comparative Analysis
Composition Comparison
- DB6 Steel: Contains alloying elements like chromium, molybdenum, and vanadium, which enhance its toughness and resistance to heat and wear.
- High Carbon Steels: Primarily rely on carbon content for their hardness and strength without significant alloying additions.
Hardness and Toughness
- DB6 Steel: While DB6 may not be as hard as high carbon steels, it offers excellent toughness, making it ideal for high-stress industrial uses.
- High Carbon Steels: These steels are extremely hard but less tough, which makes them prone to cracking under extreme conditions.
Wear Resistance
- DB6’s alloyed structure offers superior wear resistance in high-temperature environments.
- High carbon steels provide moderate wear resistance but may degrade under high heat.
Machinability and Workability
- DB6 Steel: Offers good machinability and can be worked into complex shapes.
- High Carbon Steels: More challenging to machine due to their hardness.
Strength and Durability: DB6 vs. High Carbon Steels
DB6 Steel Strength Under Stress:
DB6’s robust toughness makes it ideal for repeated use in high-impact, high-heat scenarios, such as die-casting or extrusion.
High Carbon Steel Performance in High-Stress Environments:
While high carbon steels excel in strength, they are less durable in prolonged high-temperature environments, making them unsuitable for hot work applications.
Heat Treatment: DB6 vs. High Carbon Steels
Heat Treatment Process of DB6 Steel
DB6 is subjected to quenching and tempering processes, which give it optimal toughness and hardness for die applications.
Heat Treatment Process of High Carbon Steels
High carbon steels undergo annealing, hardening, and tempering to achieve high hardness levels.
Differences in Heat Treatment Outcomes
- DB6 retains toughness even after heat treatment.
- High carbon steels become extremely hard but lose some toughness in the process.
Corrosion Resistance
DB6 Steel’s Resistance to Corrosion:
DB6 has better corrosion resistance compared to high carbon steels due to its alloying elements like chromium.
High Carbon Steel’s Corrosion Limitations:
High carbon steels are more prone to rusting and corrosion when exposed to moisture or corrosive environments.
Conclusion
Choosing between DB6 steel and high carbon steels depends entirely on your application. If you need a material with excellent toughness, heat resistance, and wear performance, DB6 steel is your best bet. On the other hand, if cost and hardness are primary considerations, high carbon steels might meet your requirements.
FAQs
1. What is the biggest difference between DB6 and high carbon steels?
The biggest difference lies in their composition. DB6 is an alloyed tool steel, while high carbon steels rely on carbon for their properties.
2. Which steel is better for die and tooling?
DB6 is superior for die and tooling due to its heat resistance and toughness.
3. How do DB6 and high carbon steels respond to heat treatment?
DB6 retains toughness after heat treatment, whereas high carbon steels become extremely hard but lose toughness.
4. Is DB6 steel more expensive than high carbon steel?
Yes, DB6 steel is typically more expensive due to its alloying elements and superior properties.
5. Can high carbon steel replace DB6 in industrial applications?
High carbon steel can be used for specific low-temperature applications, but it cannot match DB6’s performance in hot work environments.
Discover the quality of Die Steel with VIRAT SPECIAL STEELS PVT. LIMITED. Get in touch with us today to place your requirement! Contact us today to buy the best quality DB6 / DIN 2714 steel for your tooling needs! https://www.viratsteels.com/din-2714.html
Any further queries feel free to contact us :
🌐https://www.viratsteels.com 📩info@viratsteels.com 📲+91-98140-21775