AISI H13
now browsing by tag
What is H13 Steel and Its Applications?
Introduction
When it comes to materials that can withstand extreme conditions, H13 steel stands out as a top contender. This versatile chromium-molybdenum hot work tool steel is renowned for its exceptional combination of toughness, hardness, and resistance to thermal fatigue. Its unique properties make it indispensable across various industries, from automotive to aerospace.
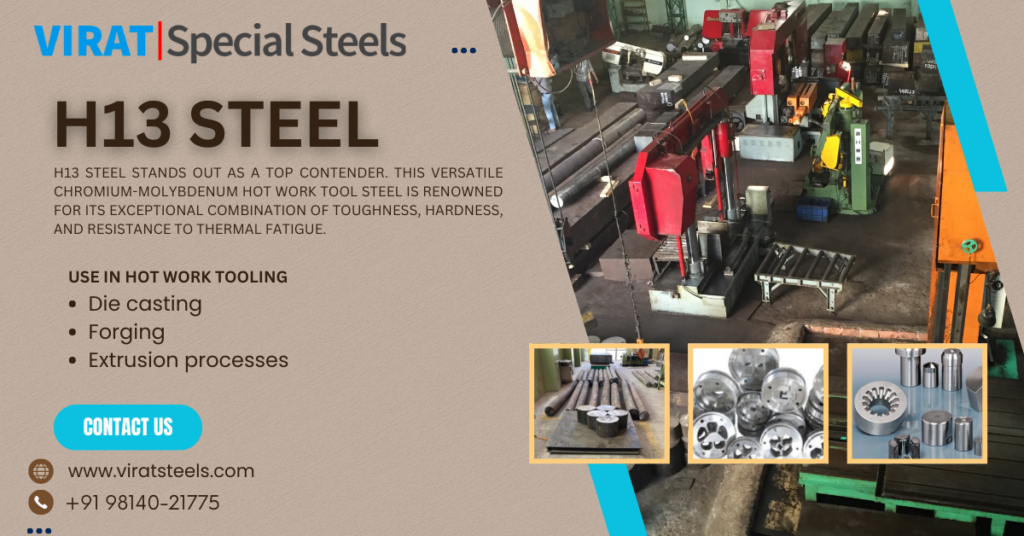
Chemical Composition of H13 Steel
The remarkable characteristics of H13 steel are rooted in its specific chemical makeup. The typical composition includes:
- Carbon (C): 0.32 – 0.40%
- Chromium (Cr): 5.13 – 5.25%
- Molybdenum (Mo): 1.33 – 1.4%
- Vanadium (V): 1.0%
- Silicon (Si): 1.0%
- Manganese (Mn): 0.20 – 0.50%
Each element plays a pivotal role:
- Carbon enhances hardness and strength.
- Chromium improves hardenability and resistance to oxidation.
- Molybdenum increases toughness and high-temperature strength.
- Vanadium contributes to wear resistance and grain refinement.
- Silicon boosts strength and elasticity.
- Manganese aids in deoxidation during steel production.
This balanced composition ensures that H13 steel maintains its integrity under demanding conditions.
Physical Properties of H13 Steel
Understanding the physical properties of H13 steel provides insight into its performance in various applications:
- Density: Approximately 7.80 g/cm³ (0.282 lb/in³)
- Thermal Conductivity: 24.3 W/m-K at 215°C (419°F)
- Coefficient of Thermal Expansion: 11.0 µm/m-°C between 25°C and 95°C
These properties indicate that H13 steel can efficiently conduct heat while maintaining dimensional stability, crucial for tools exposed to rapid temperature changes.
Mechanical Properties of H13 Steel
The mechanical prowess of H13 steel is evident in its ability to withstand substantial stress without deformation:
- Hardness: Rockwell C scale hardness ranges from 28 to 53, depending on heat treatment.
- Tensile Strength: Ultimate tensile strength can reach up to 1990 MPa (289,000 psi).
- Toughness: Demonstrates excellent toughness, essential for resisting cracking under impact.
These attributes make H13 steel suitable for applications requiring both strength and durability.
Heat Treatment Processes for H13 Steel
To optimize its properties, H13 steel undergoes specific heat treatment processes:
- Annealing: Heating to 1550°-1650°F, holding until uniformly heated, then cooling slowly to about 1000°F to soften the steel for machining.
- Hardening: Heating to 1800°-1850°F, followed by air or oil quenching to achieve desired hardness.
- Tempering: Reheating to 1000°-1150°F, depending on the required hardness, to reduce brittleness.
These treatments enhance the steel’s performance in various applications.
Advantages of Using H13 Steel
H13 steel offers several notable benefits:
- High-Temperature Resistance: Maintains strength and hardness at elevated temperatures, making it ideal for hot work applications.
- Wear Resistance: The presence of vanadium carbides provides excellent resistance to abrasion.
- Thermal Fatigue Resistance: Can withstand repeated heating and cooling cycles without cracking.
These advantages contribute to its widespread use in demanding environments.
Applications
1. Applications in Hot Work Tooling
H13 steel is widely used in hot work tooling applications where materials are subjected to high temperatures and extreme mechanical stress. Some of its key applications in this domain include:
- Die Casting Dies: H13 steel is commonly used for die-casting dies due to its excellent heat resistance, wear resistance, and toughness. The ability to withstand the rapid heating and cooling cycles involved in die-casting operations ensures longer tool life.
- Extrusion Dies: In aluminum and other metal extrusion processes, H13 steel is used to manufacture dies that shape and form metal billets. The steel’s strength and thermal stability prevent premature wear and deformation.
- Forging Dies: H13 steel is used in the production of forging dies that shape metal parts through high-pressure impacts. The toughness and heat resistance of H13 help the dies maintain their shape under extreme conditions.
These applications make H13 an indispensable material in the hot work tooling industry, ensuring efficiency, precision, and durability.
2. Applications in Cold Work Tooling
Although primarily known for hot work applications, H13 steel also finds limited usage in cold work tooling where wear resistance and impact strength are required. Some examples include:
- Shear Blades: H13 steel is used for manufacturing shear blades that cut or trim metal sheets, where its hardness and durability contribute to precision and long service life.
- Stamping Dies: H13 is occasionally used in stamping dies for cold-forming applications, where its wear resistance helps maintain die integrity.
- Plastic Molds: While more common in hot work environments, H13 is also used for plastic injection molding where high strength and heat resistance are necessary.
Although other cold work steels like D2 or O1 may be preferred for most cold work applications, H13’s versatility allows it to be used where both wear resistance and toughness are required.
3. Use in Plastic Injection Molding
H13 steel is one of the top choices for plastic injection molding tools, particularly for mold inserts. Some advantages include:
- High Thermal Conductivity: Ensures efficient heat dissipation, reducing cycle times and improving productivity.
- Wear and Corrosion Resistance: Prevents mold degradation, ensuring longevity and consistent production quality.
- Dimensional Stability: H13 maintains its structure under high pressure and temperature, reducing warping and defects in molded parts.
These properties make H13 a preferred material for injection molding applications, where durability and precision are critical.
4. H13 Steel in the Automotive Industry
The automotive sector relies on H13 steel for various high-performance applications. Some of the most common uses include:
- Engine Components: H13 steel is used in manufacturing engine components such as cylinder heads, pistons, and exhaust valves, where high-temperature resistance is necessary.
- Structural Parts: Some automotive manufacturers use H13 in critical structural components that must withstand mechanical and thermal stress.
- Tooling for Manufacturing: Many of the dies and molds used in automotive production, including stamping dies and injection molds, are made from H13 steel.
The exceptional properties of H13 steel help improve the durability and performance of automotive parts and manufacturing processes.
5. H13 Steel in the Aerospace Industry
The aerospace industry demands materials with superior strength, heat resistance, and toughness. H13 steel meets these requirements and is used in:
- Turbine Blades: Due to its heat resistance, H13 is used in manufacturing certain aerospace turbine components exposed to high temperatures.
- Structural Components: Some aerospace structures, including landing gear and support brackets, benefit from the toughness of H13 steel.
With the aerospace industry constantly pushing for high-performance materials, H13 remains a strong candidate for demanding applications.
Conclusion
H13 steel is a versatile and high-performance material used in numerous industries, including automotive, aerospace, die-casting, and injection molding. Its unique combination of high-temperature resistance, wear resistance, and toughness makes it an ideal choice for hot work tooling and other demanding applications. While it has some limitations, proper heat treatment and machining techniques help maximize its benefits. Whether in the production of industrial tools, aerospace components, or plastic molds, H13 remains a top-tier tool steel for high-performance applications.
Mode of Supply
Virat Special Steels is the largest stockiest and supplier of H13 tool steel in flat, square and round bar. We provide steel in all sizes as your requirements. H13 die steel is available in flat, square and round shape. Consult our team who will assist you for h13 steel query.
FAQs
1. What makes H13 steel suitable for high-temperature applications?
H13 steel has excellent thermal fatigue resistance, high wear resistance, and superior toughness, making it ideal for high-temperature applications such as die casting and forging.
2. How does H13 steel compare to D2 tool steel?
H13 is better suited for high-temperature applications, while D2 is a cold work steel with superior wear resistance. Choosing between them depends on whether heat resistance or abrasion resistance is a priority.
3. Can H13 steel be welded?
Yes, H13 steel can be welded, but it requires preheating and post-weld heat treatment to prevent cracking and ensure structural integrity.
4. What industries commonly use H13 steel?
H13 steel is widely used in die-casting, plastic injection molding, aerospace, automotive manufacturing, and hot work tooling applications.
5. How does heat treatment affect H13 steel?
Proper heat treatment enhances H13 steel’s hardness, strength, and resistance to thermal fatigue, ensuring optimal performance in demanding applications.
H13 Steel for Die Casting: Key Benefits You Should Know
H13 steel stands as a cornerstone in the die casting industry. Known for its exceptional heat resistance and toughness, this versatile hot-work tool steel is widely used in demanding environments. As die casting often involves high-pressure and extreme thermal conditions, choosing the right material for dies is critical. Enter H13 steel – the ultimate material to enhance durability, improve performance, and maximize efficiency in casting operations.
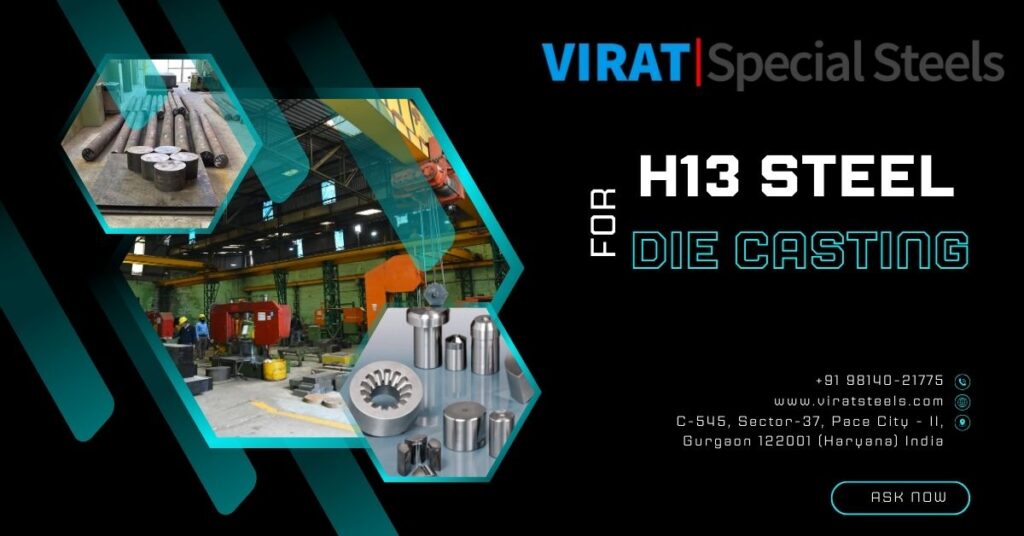
What sets H13 steel apart from the rest? Its outstanding properties make it highly sought after for both small-scale and large-scale die casting applications. But let’s dig deeper into what makes it so special.
Composition and Properties of H13 Steel
Chemical Composition
H13 steel is an alloy comprising a mix of critical elements that optimize its performance. Here’s a breakdown of its main components:
- Chromium (5%): Enhances corrosion resistance.
- Molybdenum (1.4%): Improves hardness and high-temperature strength.
- Vanadium (1%): Increases wear resistance and toughness.
- Carbon (0.4%): Adds strength and hardenability.
- Silicon (1%): Boosts resistance to oxidation.
Mechanical Properties
H13 steel is known for its high tensile strength, ductility, and excellent thermal conductivity. These properties ensure the material remains reliable under rigorous operating conditions. Additionally, H13 steel demonstrates impressive hardenability, making it an ideal choice for precision die applications.
What Makes H13 Steel Ideal for Die Casting?
Thermal Stability
One of the standout features of H13 steel is its remarkable thermal stability. In die casting, molds must endure rapid temperature fluctuations without cracking or deforming. H13’s ability to retain strength at elevated temperatures makes it indispensable.
Resistance to Thermal Fatigue
When dies repeatedly heat and cool during the casting cycle, they are prone to thermal fatigue. H13 steel offers resistance to such stresses, extending the lifespan of the tooling and reducing operational downtime.
Key Benefits of H13 Steel in Die Casting
1. Durability Under High Temperatures
Die casting requires materials that can handle intense heat without losing integrity. H13 steel delivers exceptional performance in such scenarios, maintaining structural stability even under prolonged exposure to molten metals.
2. Excellent Wear Resistance
The abrasive nature of die casting operations can wear down weaker materials quickly. With its robust wear resistance, H13 steel minimizes maintenance needs and offers long-lasting performance.
3. Cost-Effectiveness in Long Production Runs
Although the initial investment in H13 steel may be higher, its durability and resistance to damage translate into significant cost savings over time. Long production cycles benefit greatly from its ability to perform without frequent replacements or repairs.
Longevity and Durability of H13 Steel Dies
Improved Tool Life
When it comes to tooling materials, longevity matters. H13 steel excels in providing longer service life, reducing the need for frequent replacements. Its resilience against wear and deformation significantly adds to the efficiency of the production process.
Resistance to Deformation
Under the extreme pressures of die casting, lesser materials may deform, leading to suboptimal casting results. H13 steel’s resistance to deformation ensures precision and repeatability across countless cycles.
Challenges and Limitations of H13 Steel
Cost Considerations
While H13 steel is cost-effective in the long run, its upfront cost may deter smaller manufacturers. Investing in H13 tooling requires foresight and planning to maximize its return on investment.
Potential Limitations in Specific Environments
H13 steel thrives under high temperatures, but in applications involving extremely corrosive materials or environments, alternative alloys with specific properties might be better suited.
Future Trends in Die Casting Using H13 Steel
Advances in Steel Technologies
Research and innovation are leading to improved formulations of H13 steel with enhanced properties like higher thermal resistance and lower environmental impact. Such developments will further cement H13’s place in the future of die casting.
Emerging Applications and Industries
With rapid advancements in technology, H13 steel’s applications are expanding beyond traditional die casting. Sectors like robotics and renewable energy are beginning to explore its potential, showcasing the steel’s enduring versatility.
Conclusion
H13 steel has revolutionized the die casting industry with its unmatched thermal stability, wear resistance, and adaptability. From improving tool longevity to delivering consistent, high-quality results, it’s clear why this alloy is the material of choice for demanding casting operations. By investing in H13 steel, manufacturers can elevate their production standards, reduce costs over time, and lead the way in sustainable manufacturing.
FAQs
1. Why is H13 steel commonly used in die casting?
H13 steel is ideal for die casting due to its thermal stability, resistance to wear and deformation, and long service life. It is especially effective in high-temperature, high-pressure applications.
2. Can H13 steel be recycled?
Yes, H13 steel is 100% recyclable, making it a sustainable choice for manufacturers committed to reducing waste.
3. How does H13 steel compare to P20 steel?
H13 steel offers superior heat resistance and durability compared to P20, making it more suitable for demanding die casting operations.
4. What industries use H13 steel dies?
H13 steel is widely used in industries such as automotive, aerospace, electronics, and general manufacturing for creating precision die-cast components.
5. What maintenance is required for H13 steel dies?
Regular preventive maintenance, including cleaning, inspections, and refurbishments, is essential to extend the lifespan of H13 steel dies and ensure optimal performance.
Virat Special Steels: A Leader in H13 Steel Supplies
Virat Special Steels is a renowned name in delivering high-quality tool steels, including H13. With decades of industry expertise, Virat has built a reputation for reliability and superior service. Industries across automotive, aerospace, and plastic molding trust Virat for their steel requirements.
Virat Special Steels is the largest Supplier & Stockiest of H13 Steel in India. Consult our team who will assist you for H-13/ DIN 2344 / AISI H13 steel query. https://www.viratsteels.com/h13.html
Size Range in Forged / Rolled Bars:
Rounds: 13mm Dia to 1500mm Dia
Rectangular: Thickness 13mm – 500mm / Width 13mm to 1500mm
For more information or to discuss your steel needs, Virat Special Steels invites you to reach out through their contact details provided, ensuring a professional and informative experience.
Any further queries feel free to contact us :
🌐https://www.viratsteel.in 📬 info@viratsteels.com ☎+91 98140-21775